In the realm of manufacturing, ensuring products consistently perform well is crucial. From stress screening to ongoing reliability testing, this article explores the various tests that identify potential issues, assess durability, and enhance the quality of manufactured items. Read on to understand how these reliability testing contributes to creating long-lasting products in the competitive manufacturing industry.
What Is Reliability Testing?
Reliability testing is a methodical process used to assess and ensure the consistent performance and durability of products, helping you improve product quality, performance, and customer satisfaction. This testing involves subjecting items to various conditions and stresses that simulate real-world usage.
By doing so, manufacturers can identify potential weaknesses, defects, or points of failure in a product before it reaches the market. Reliability Testing aims to enhance the overall quality and dependability of manufactured goods, assuring consumers that the products will perform as intended over an extended period.
What Is An Example of A Reliability Test?
An example of a reliability test is subjecting a product to Environmental Stress Screening (ESS). In this test, the product undergoes conditions like temperature variations, vibrations, and humidity levels that simulate a range of environmental challenges. ESS helps identify potential defects or weaknesses in the product, ensuring it can perform reliably under different circumstances. This type of reliability test is valuable for manufacturers to confirm the product’s dependability and its ability to withstand various stressors before reaching the market.
How Do You Check The Reliability of The Product?
Assessing the reliability of a product involves a systematic evaluation to ensure that it consistently performs as expected over time. This process is crucial to identify potential issues and ensure the product meets quality standards.
1. Reliability Test Planning
Reliability Test Planning outlines the protocol for testing a product. During this phase, the team creates a detailed plan to guide the entire testing process. Key considerations include defining the testing criteria, setting performance standards, and determining the testing timeline. This planning stage ensures that the team structures the subsequent reliability tests with purpose and aligns them with the project’s overall objectives.
2. Reliability Test Strategies
Engineers develop Reliability Test Strategies by creating a clear plan for the testing approach and repeatedly executing the same set of tests on the system to assess its consistency and reliability. This includes outlining the overall approach based on the nature of the product, potential failure modes, and desired testing outcomes.
These test strategies act as guiding principles for subsequent steps, helping align testing activities with the overall goals of the project. Establishing reliable strategies ensures a systematic and purposeful execution of the reliability testing process.
3. Environmental Testing
Environment testing involves creating conditions that mimic the real-world scenarios in which a product will be used to evaluate a product’s ability to function in conditions like temperature, humidity, vibration, shock, dust, and water. This step is crucial for assessing how the product performs in various situations and environments.
Environmental testing ensures that the reliability testing accurately replicates the conditions the product is expected to face during its lifecycle. By establishing a suitable test environment, manufacturers can identify potential weaknesses and evaluate the product’s ability to function consistently in different scenarios.
4. Accelerated Life Tests
Accelerated Life Tests (ALT) is the process of testing a product by subjecting it to conditions (stress, strain, temperatures, voltage, vibration rate, pressure, etc.), intentionally subjecting a product to extreme conditions and stress levels to simulate an extended period of use in a shorter time frame.
The goal is to assess how the product performs under accelerated stress, allowing manufacturers to predict potential failures and weaknesses that might occur over an extended period of normal usage.
Single Stress
In Single-stress ALT, the product is exposed to only one specific type of extreme condition or stress. This could be elevated temperatures, high voltage, intense vibration, or other factors. This method helps identify how the product responds to a single stressor and allows manufacturers to pinpoint weaknesses related to that particular stress.
Multiple Stress
Multiple Stress ALT involves subjecting the product to a combination of different stress factors simultaneously. This method simulates real-world scenarios where products may experience a variety of stressors concurrently. It helps manufacturers understand how the product performs under more complex and diverse conditions.
Sequential Stress
Sequential Stress ALT involves exposing the product to a series of stress levels in a step-by-step fashion. The stress levels gradually increase, allowing manufacturers to observe how the product reacts to escalating conditions. This method helps identify the threshold at which the product may fail or exhibit weaknesses over a range of stress levels.
Step Stress
In Step Stress ALT, the product is subjected to increasing levels of stress in distinct steps or stages. At each step, the stress level is raised incrementally. This method is useful for determining how the product responds to gradual increases in stress over time, helping identify potential failure points or weaknesses during the step-wise progression.
5. Discovery Testing
Discovery testing in reliability testing involves systematically subjecting a product to various conditions and stresses to identify potential weaknesses or defects. Better named a discovery or exploratory process, this type of testing involves running experiments, applying stresses, and doing ‘what if?’ type probing.
This phase aims to uncover any issues early in the product development process. By observing how the product responds to different stresses, manufacturers can pinpoint areas that may require improvement or modification.
HALT (Highly Accelerated Life Test)
HALT is a method where a product is subjected to extreme conditions and stress levels to identify its limits and weaknesses. This involves exposing the product to rapid temperature changes, intense vibrations, and other extreme environmental conditions to discover potential failure points.
Margin Test
The Margin Test evaluates a product’s performance at the extremes of its specifications. It aims to assess how well the product functions when pushed to its limits. By intentionally operating the product near its maximum capabilities, manufacturers can understand its safety margins and identify potential issues under stress.
Sample Size of 1
This involves testing a single unit (sample size of 1) rather than multiple units. By focusing on a single product, manufacturers can gain insights into individual unit performance and discover any unique issues that may arise. While traditional testing involves multiple samples, a Sample Size of 1 is a targeted approach to identify specific challenges in individual units during discovery testing.
6. Reliability Growth Testing
Reliability Growth Testing is a systematic process aimed at improving the reliability of a product over time, supporting improvements in system and component Reliability over time through a systematic process of stressing the system to identify failure modes and design weaknesses.
The testing involves conducting iterative cycles of testing, analyzing the results, and making necessary improvements. This testing method helps identify and address any reliability issues that may arise during the product’s development. The cycle typically includes
1. Test
This initial phase involves subjecting the product to various stressors and conditions to identify potential failure modes and weaknesses. Testing aims to simulate real-world scenarios and assess how the product performs under different conditions.
2. Analyze
After testing, the collected data is thoroughly analyzed to identify any failures, trends, or patterns. The goal is to understand the product’s performance, pinpoint weaknesses, and gain insights into the root causes of any reliability issues.
3. Fix (TAAF – Test-Analyze-Fix)
Based on the analysis, necessary improvements and modifications are made to address identified weaknesses. This step involves fixing design flaws, manufacturing issues, or any other factors contributing to reliability concerns. The goal is to enhance the product’s reliability.
4. Duane
The Duane model is a statistical approach used in reliability growth testing. It helps in predicting future failures based on the observed data during testing. The model assists in estimating when reliability goals will be achieved and provides insights into the product’s overall reliability improvement over time.
8. Software Testing
This step assesses the reliability of software components through White-box testing (examining internal structures), Black-box testing (evaluating functional aspects), Operational Profile testing (considering real-world usage scenarios), and Fault Injection (introducing deliberate faults for assessment).
9. Product Testing
Product testing involves evaluating the entire product to ensure it performs as intended and meets specific standards, helping to predict future behavior during the complete life cycle of the product, component, or material under test.
This comprehensive testing assesses the integrated performance of all components, examining how they work together under various conditions. The goal is to identify any potential issues or weaknesses in the product’s design, functionality, or reliability. Product testing is a crucial step in the development process to guarantee that the final product aligns with performance expectations and quality standards before reaching the market.
10. Qualification/Demonstration Testing
Qualification/Demonstration Testing involves conducting tests to confirm that a product meets predetermined standards and specifications. Engineers systematically evaluate and verify whether the product or component meets the required specifications, standards, and performance criteria before releasing it into the market.
The qualification testing phase verifies the product’s performance, functionality, and reliability, ensuring that it aligns with the defined criteria. It serves as a demonstration of the product’s capabilities, assuring stakeholders that the product meets the necessary qualifications before it is released to the market.
This testing process is critical for establishing the product’s compliance with set standards and ensuring it is ready for deployment or use.
Sequential Tests
Sequential tests involve a step-by-step assessment of a product’s performance. Each step focuses on specific aspects or criteria, allowing for a systematic and thorough evaluation of the product. This method ensures that the product undergoes a sequence of tests, each serving a unique purpose in verifying its compliance with standards and specifications.
Fixed-length Tests
Fixed-length tests have a predetermined duration or set timeframe for evaluation. During this fixed period, the product is subjected to testing conditions to assess its performance and reliability. This approach provides a standardized way of measuring the product’s capabilities within a specified time frame, contributing to a comprehensive evaluation as part of the qualification testing process.
11. Product Reliability Acceptance Testing (PRAT)
Product Reliability Acceptance Testing (PRAT), which usually involves the testing of a sample of items drawn from a production batch or lot, is the process of evaluating and confirming that a product meets the required reliability standards and criteria set by the customer or regulatory authorities.
The PRAT phase occurs after the product has undergone various assessments, including qualification testing. PRAT focuses specifically on reliability aspects, ensuring that the product is dependable and performs reliably under expected conditions. Successful completion of Product Reliability Acceptance Testing indicates that the product has met the reliability requirements.
12. Ongoing Reliability Testing
Ongoing Reliability Testing is a continuous and long-term process aimed at monitoring and ensuring the sustained reliability of a product throughout its life cycle. This involves periodically subjecting the product to testing conditions to detect any potential issues or degradation in performance over time.
One example of ongoing reliability testing is the sequential probability ratio test (SPRT), where engineers use this statistical method to assess whether the product’s performance remains within acceptable limits over time. It involves regularly collecting data during the product’s operation and statistically analyzing the results.
13. Stress Screening
Stress screening in reliability testing is a form of deliberately intense or thorough testing, used to identify and eliminate potential defects or weaknesses in a product by subjecting it to extreme conditions. The process of applying mechanical, electrical, and/or thermal stresses to an equipment item to precipitate latent parts and workmanship defects to early failure. This involves exposing the product to heightened levels of stress, such as increased temperature, vibration, or other environmental factors. The goal is to simulate more intense conditions than the product is expected to encounter during normal use.
ESS (Environmental Stress Screening)
ESS involves exposing the product to a range of environmental conditions such as temperature variations, vibrations, and humidity. The screening process uncovers latent defects that may arise under different environmental stresses. Manufacturers apply ESS during the early stages of production to identify and eliminate potential issues before the product reaches the customer.
HASS (Highly Accelerated Stress Screening)
HASS is a stress screening method where the product undergoes intense stress conditions, typically higher than what it would encounter in normal use. The purpose is to quickly identify any manufacturing or design flaws. Manufacturers conduct HASS on a sample basis during production to detect and address issues before mass production.
Burn-in Tests
Burn-in tests involve operating the product continuously under normal or slightly elevated operating conditions for an extended period. This process helps identify potential failures that may occur during the early stages of use. Burn-in tests are particularly useful for detecting infant mortality issues and ensuring the product’s reliability over time.
14. Attribute Testing
Reliability testing uses attribute testing to assess whether a product has specific characteristics or attributes. Instead of measuring quantitative values, this testing focuses on qualitative traits.
It involves determining whether certain features meet predefined criteria or conform to specified standards. Attribute Testing is valuable for evaluating the reliability of specific aspects within a product, helping identify and address any deviations from the expected attributes.
Binomial
Binomial testing is employed when assessing the success or failure of a particular attribute in a product. It is particularly useful for situations where there are only two possible outcomes, such as pass or fail. The Binomial distribution helps determine the probability of observing a certain number of successes in a fixed number of trials, providing insights into the attribute’s reliability.
Hypergeometric
We apply hypergeometric testing when drawing a sample from a finite population without replacement. This method is suitable for situations where the presence of a specific attribute in the sample is of interest. Hypergeometric distribution helps calculate the probability of obtaining a certain number of items with the desired attribute in a sample drawn from a population without replacement.
15. Degradation (Wear to Failure) Testing
Engineers use degradation (wear to failure) testing to evaluate how a product’s performance changes over time due to wear and tear. They consider a piece of equipment to have failed when the degradation value crosses a certain threshold level.
Instead of abruptly causing failure, this testing process involves subjecting the product to gradual and continuous stress to simulate real-world conditions. The goal is to observe the product’s deterioration until it reaches a point where it can no longer function effectively.
This form of testing helps identify the rate at which the product degrades and provides valuable insights into its expected lifespan and performance under extended use.
In summary, reliability testing plays a vital role in helping organizations maintain their operational processes and ensure the integrity of their assets. By thoroughly examining products, companies not only guarantee that their offerings perform consistently but also strengthen their overall operations. The insights gained from these tests allow organizations to proactively address potential issues, minimize risks, and uphold the reliability of their assets.
Join PetroSync Training for Practical, Real-World Insights
Moreover, for those seeking to deepen their understanding of reliability testing, consider enrolling in the Certified Reliability Engineer training offered by PetroSync. This comprehensive program equips you with the knowledge and skills necessary to navigate the intricacies of reliability testing, covering a wide array of methodologies and best practices.
By enrolling in CRE training, you not only enhance your proficiency in conducting reliable assessments but also contribute to elevating the overall reliability standards within your organization. Take this opportunity to invest in your professional development, positioning yourself as a valuable engineer in the dynamic field of reliability testing and reinforcing the foundation of your organization’s operational and asset integrity.
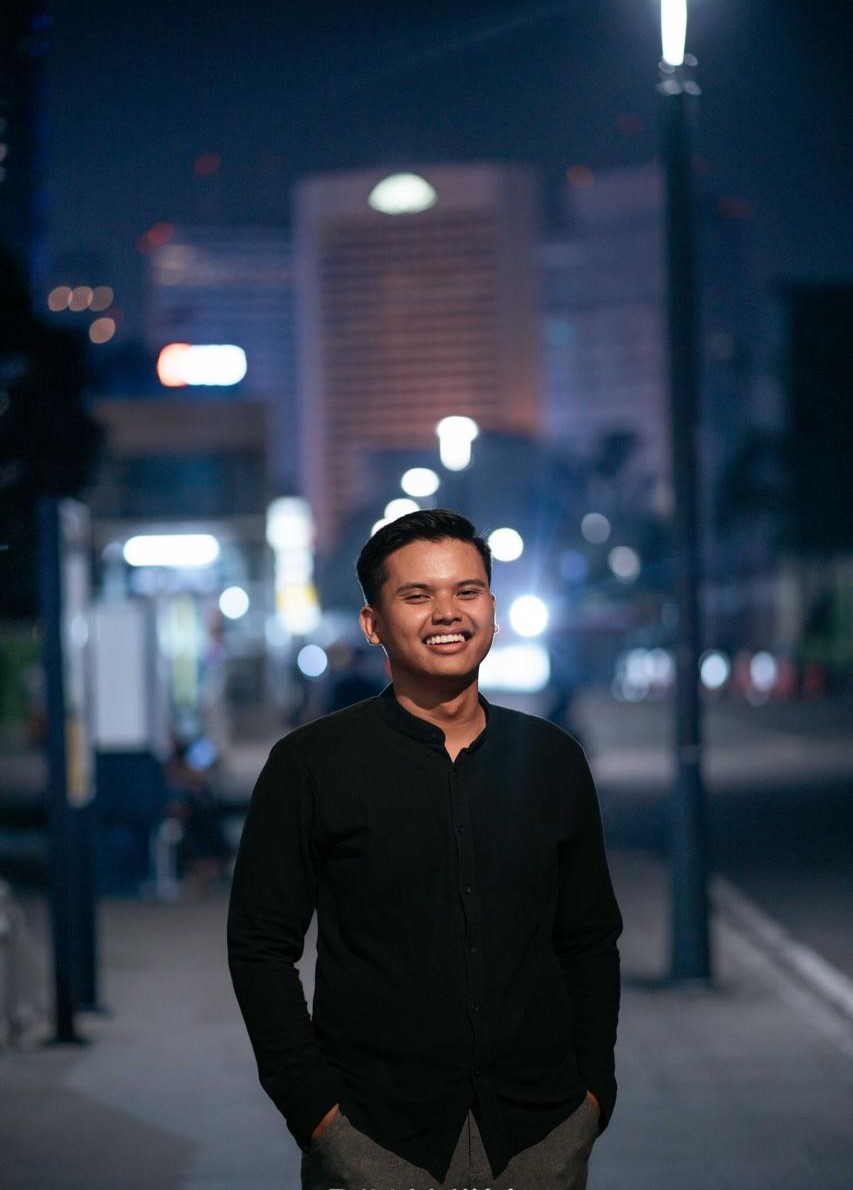
Results-oriented and thorough SEO specialist with extensive experience in conducting keyword research, developing and implementing digital website promotion strategies and plans, managing campaigns to develop company websites in the digital world, excellent knowledge of marketing techniques and principles, and attentive strong attention to detail.