The impact of shutdowns in the industrial sector on plant productivity is a topic of significant importance. A shutdown, or temporary cessation of operations, within an industrial plant can have profound effects on overall productivity.
What Is Shutdown in Engineering?
In engineering, a shutdown refers to a planned and systematic cessation of operations within a plant—a time where production halts. This temporary pause is carefully orchestrated to facilitate essential maintenance, repair, or modification activities, ensuring the continued optimal functioning of equipment and systems.
Shutdowns are pivotal events strategically designed to enhance overall performance and reliability. During these periods, engineers and maintenance teams meticulously inspect, repair, and upgrade machinery, proactively preventing unexpected breakdowns. This proactive approach not only contributes to the longevity of the engineering systems but also maximizes operational efficiency.
Shutdowns are thoughtfully scheduled to minimize disruption to regular operations while maximizing the benefits of the maintenance activities, forming an integral part of a plant’s comprehensive operational strategy.
What Are Some Types of Shutdown in Industry?
In general, there are several types of shutdown your plants may undergo:
1. Planned Shutdowns
Planned industrial shutdowns are scheduled events carefully arranged in advance to facilitate essential maintenance, repair, or modification tasks. These planned downtimes allow the maintenance crew to address issues that may have arisen since the last shutdown efficiently.
With a thorough list of tasks prepared, these scheduled pauses in operations provide a well-organized environment for the team to work through maintenance challenges in a timely and efficient manner, ensuring the continued optimal functioning of the plant.
2. Emergency Shutdowns
Emergency shutdowns, in contrast, are unscheduled halts to operations that occur abruptly, often in response to equipment failure. While unplanned and potentially frustrating, these shutdowns, if conducted according to established protocols, aim to happen quickly and in a controlled manner. The primary goal is to minimize the risk of accidents during the unexpected chaos, demonstrating the importance of having well-defined emergency shutdown procedures in place.
3. Partial Shutdowns
Partial shutdowns involve allowing part of a plant to remain operational in some capacity while other sections undergo maintenance or repair. These types of shutdowns are often associated with emergency situations, introducing additional challenges for startup and maintaining product quality. Despite the complexity, partial shutdowns enable the plant to continue some level of production, mitigating the impact of the maintenance activities on overall operations.
4. Full Shutdowns
A full shutdown signifies a complete halt to day-to-day operations. These comprehensive pauses are typically planned events with a detailed list of tasks to complete. During a full shutdown, the entire plant undergoes maintenance, allowing the maintenance crew to address a wide range of issues and ensure the thorough upkeep of equipment and systems. This planned approach contributes to the long-term reliability and efficiency of the industrial facility.
How To Plan Industrial Shutdown?
There are some structural steps to plan for industrial shutdown to get the most out of it:
1. Strategic Scheduling
Planning an industrial shutdown begins with strategic scheduling. This involves identifying optimal times for the shutdown, considering factors such as production demand, equipment performance, and workforce availability. By aligning the shutdown with periods of lower demand or when critical machinery can be spared, the impact on overall operations is minimized.
2. Task Prioritization
Once the shutdown period is established, the next step is task prioritization. Maintenance crews must compile a thorough list of tasks to be accomplished during the shutdown. Prioritizing these tasks ensures that critical maintenance, repair, and inspection activities are addressed first, maximizing the efficiency of the downtime.
3. Resource Allocation
Effective resource allocation is crucial in planning an industrial shutdown. This includes determining the necessary manpower, materials, and tools required for the maintenance tasks. Ensuring that all resources are readily available and properly organized streamlines the execution of planned activities during the shutdown period.
4. Communication and Coordination
Communication and coordination play a pivotal role in successful shutdown planning. All stakeholders, including maintenance teams, production staff, and management, should be well-informed about the upcoming shutdown. Clear communication channels help mitigate disruptions and ensure everyone is aligned with the shutdown plan.
5. Contingency Planning
Anticipating unforeseen challenges is an integral part of planning an industrial shutdown. Contingency planning involves identifying potential risks and developing strategies to address them promptly. This proactive approach helps minimize downtime and ensures a smooth and controlled shutdown even when unexpected issues arise.
6. Safety Measures
Ensuring the safety of personnel and equipment is paramount during an industrial shutdown. Implementing comprehensive safety measures, including training programs, safety protocols, and emergency response plans, contributes to a secure working environment during maintenance activities.
7. Documentation and Reporting
Thorough documentation and reporting are essential components of a well-planned industrial shutdown. Maintaining detailed records of completed tasks, inspections, and any issues discovered during the shutdown provides valuable insights for future planning. This documentation aids in continuous improvement and enhances the effectiveness of subsequent shutdowns.
The last step is to examine the activities that occurred during the shutdown. It is advisable to generate a report summarizing your observations and insights. This report should encompass:
- Identifying the successful aspects of the shutdown.
- Recognizing the challenges or shortcomings encountered.
- Proposing potential enhancements for future shutdowns.
- Summarizing risks and detailing their management or containment.
- Completing a checklist that comprehensively covers all carried-out tasks.
By meticulously following these steps in the planning process, industrial facilities can execute well-organized and efficient shutdowns, ultimately contributing to the reliability and longevity of their equipment and systems.
In summary, shutdowns in industries are crucial for maintaining operational efficiency and safety. Properly planning and executing these pauses in operations ensure that maintenance, repair, and inspection tasks are systematically addressed. This strategic approach, involving scheduling, task prioritization, and resource allocation, contributes to the ongoing reliability of industrial facilities. Analyzing shutdown processes and seeking continuous improvement further enhances overall efficiency.
Mastery of shutdown management is essential for preventing unexpected issues, minimizing downtime, and cultivating a resilient industrial environment. As an integral aspect of maintenance planning and scheduling, understanding industrial shutdowns is a key skill for professionals aiming to optimize operations and prolong the lifespan of industrial assets.
Recognizing the significant role of industrial shutdowns in maintenance planning and scheduling, acquiring thorough skills in this area is highly advantageous. To improve your ability to manage maintenance tasks effectively and ensure smooth industrial operations, consider enrolling in PetroSync’s Maintenance Planning and Scheduling training.
Maintenance Planning and Scheduling training is designed to provide professionals with the knowledge and tools needed to excel in planning, executing, and optimizing maintenance processes, including strategic shutdown management. By investing in this training, you will deepen your understanding of maintenance planning and enhance your capabilities in scheduling and overseeing critical shutdown events.
Elevate your expertise with PetroSync’s training to navigate the complexities of maintenance planning and scheduling successfully, contributing to sustained efficiency and reliability in industrial operations.
Credit header image: Freepik
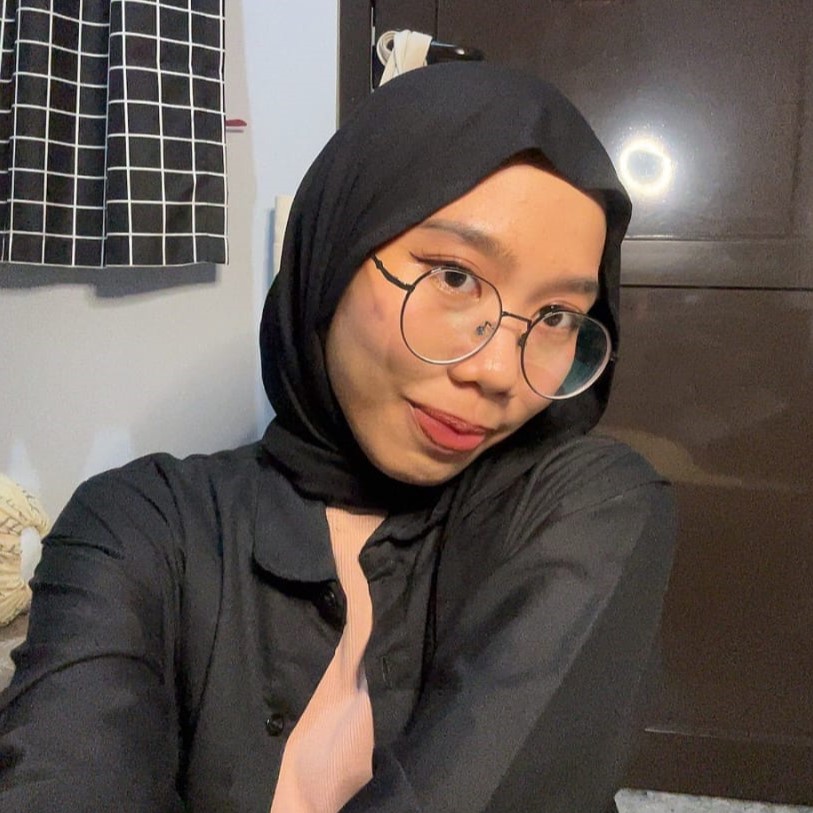
SEO specialist by day, fact-checker by night. An avid reader and content writer dedicated to delivering accurate and engaging articles through research and credible sources.