Burst testing is an essential process in engineering and materials science. Burst testing, also known as burst pressure testing, helps us understand how strong materials and products are. In this article, we will explore why burst testing matters, where it is used, and how it works.
What Is Burst Testing?
Burst testing is performed by introducing air (or other gas) into the package at a controlled rate, maintaining a constant internal pressure for a specified duration, and then examining the package for any signs of material failure. The entire package is subjected to uniform stress and failure generally reveals the weakest point.
The main goal of burst testing is to determine if the package can endure the applied pressure without any material failure or rupture. This test helps identify potential weaknesses or vulnerabilities in the package design or materials ensuring it meets safety standards and can withstand stresses during transportation and handling.
How is Burst Strength Measured?
Burst strength is the ability of a material or object (such as a metal pipe) to maintain its integrity when subjected to pressure. The burst strength is quantified in kilograms per square centimeter.
To calculate the burst factor of a corrugated or flexible package, both the burst strength and the grammage (density) of the packaging material are taken into consideration.
Burst factor = Burst Strength (kg/cm2) x 1000/Grammage (gm/m2)
To assess this, the package is expanded through the use of a rubber diaphragm or another technique until either the package or its seals rupture.
How Do You Test Bursting Strength According to the Standard?
To perform a burst test according to the ASME PCC-2 guidelines, there are several straightforward steps to follow. These steps are important because they help ensure the safety and effectiveness of materials and products used in various applications.
Proof Test Qualification Requirements
Instead of using the traditional engineered design approach, a burst test can be conducted on a mock-up buildup to assess and approve the weld buildup design. The burst test serves as an alternative method to verify the effectiveness and reliability of the weld buildup design.
1. General Requirements
A satisfactory mock-up burst test can qualify the weld buildup design for use in the same orientation, on the same type of item, and at the same location on fittings. To meet the conditions for qualification, the following criteria must be met:
- The base metal should have the same P-No. and Group number as the mock-up base material tested.
- The specified minimum tensile strength of the item should not exceed that of the mock-up base material tested.
- The average thickness of the built-up area(s) should be at least the thickness of the mock-up plug, u, in Figure 202-3-1.
- The overlap on the full thickness of the base metal, B, should be at least that of the mock-up.
- The transition angle at the outer edges of the overlay, α, should not be greater than that of the mock-up.
- The buildup surface should be similar to or smoother than that tested.
- The maximum axial dimension/diameter ratio, L/D, should not exceed that tested.
- The maximum circumferential dimension/diameter ratio, C/D, should not exceed that tested.
- The nominal diameter should be not less than one-half or more than 2 times the diameter of the mock-up tested.
- The nominal thickness/diameter ratio, t/D, should not be less than one-half or more than 3 times the t/D ratio tested.
2. Simulation of Thin Area
To replicate the area of wall-thinning during pressure testing, a rounded-corner segment of the base material in the mock-up must be removed. This represents the maximum size ratio (axial dimension of L and circumferential dimension of C) and the location of thinning or pitting that the weld buildup will compensate for.
A plug made of the same base material with a uniform thickness (u) should be fully welded around the opening and flush with the outside surface of the pressure component. Another option is to remove an equivalent volume of base metal from the inside surface of the mock-up using machining or grinding, eliminating the need for welding in a closure plug.
3. Buildup Thickness
The buildup section thickness (sum of deposit and base metal) indicated by dimensions (u) and (w) in Figure 202-3-1 should not exceed 87.5% of the nominal wall thickness for the thinned area of the mock-up. This ensures a conservative thickness to qualify the buildup design.
4. Burst Pressure
To approve a repair design for widespread use (on pressure components in the same orientation or at the same location on fittings), the burst pressure must not be lower than:
Where:
D = outside diameter of the pressure component, mm (in.)
P = minimum acceptable burst pressure, MPa (psi)
Sact = reported actual tensile strength, MPa (psi), of the base material tested
t = minimum specified thickness (excluding manufacturing tolerance) of base material tested, mm (in.)
5. Flexibility Analysis
If the original construction code necessitated flexibility analysis, the impact of the weld buildup must be evaluated about the initial analysis or validated following para. 202-3.1.3.2.
Burst Testing Method
Hydrostatic testing has the potential to result in loss of life and damage to property. It is imperative to carefully assess all tests to ensure safety and proper control of debris in the event of component failure.
1. Pump Selection
The pump station utilized for burst testing must have the capacity to surpass the maximum calculated burst pressure. The pump should be able to deliver at least 25% overpressure to accommodate variations in burst pressure due to wall thickness tolerances, weld reinforcement, and other factors. In most instances, the actual burst pressure will slightly exceed the calculated value.
What Are The Benefits of Burst Testing?
In industries like oil and gas, petrochemicals, and energy, the calculation of burst strength and conducting burst testing is essential for several reasons:
1. Safety
These industries deal with high-pressure systems and equipment, such as pipelines, pressure vessels, and storage tanks. Calculating burst strength and performing burst testing help ensure that these components can withstand internal pressure without failure or rupture, thereby reducing the risk of accidents, leaks, or catastrophic failures.
2. Compliance
Regulatory bodies often require companies in these industries to adhere to specific safety standards and guidelines. Conducting burst testing and determining burst strength is a crucial aspect of compliance, as it demonstrates that the equipment and materials used meet the required safety standards.
3. Quality Assurance
Burst testing is a critical quality assurance measure, especially during the manufacturing process of components and materials. By conducting these tests, manufacturers can verify the integrity and reliability of their products, ensuring that they meet the specified performance criteria.
4. Material Selection
Calculating burst strength and performing burst testing aid in the selection of suitable materials for different applications. It helps engineers and designers choose materials that can withstand operational pressures and environmental conditions, ensuring long-term performance and durability.
5. Preventing Costly Failures
Identifying weak points in materials through burst testing allows companies to address potential vulnerabilities before they become costly issues. It enables proactive maintenance and replacement of components, minimizing downtime and preventing expensive repairs or replacements.
6. Product Development
For new product development in these industries, burst testing is crucial to validate design concepts and ensure the safety and reliability of the final product. It helps engineers refine their designs and make necessary adjustments to meet industry requirements.
Overall, calculating burst strength and conducting burst testing are fundamental practices in these industries to ensure the safety, compliance, and quality of materials and components, thus minimizing risks and enhancing operational efficiency.
Performing accurate burst testing is essential, especially concerning safety. Industries like oil and gas, petrochemicals, and energy rely on high-pressure systems, making it crucial to ensure the reliability of components to prevent accidents and potential risks. By conducting thorough burst testing, companies ensure that only strong and dependable components are used in critical applications, preventing costly accidents, leaks, or major failures.
Adhering to strict ASME PCC-2 through proper burst testing provides companies with confidence in the reliability of their equipment, prioritizing safety and efficiency in their operations.
PetroSync offers comprehensive ASME PCC-2 training that covers essential topics, including burst testing. You can gain valuable insights into conducting burst tests to ensure the safety and reliability of pressure equipment regulated under ASME PCC-2. With PetroSync’s expert guidance, you can enhance your skills and excel in your roles within the oil and gas, petrochemical, and energy sectors by joining ASME PCC-2 training.
Get ready to enhance your knowledge and expertise in pressure equipment through PetroSync’s engaging and high-quality training.
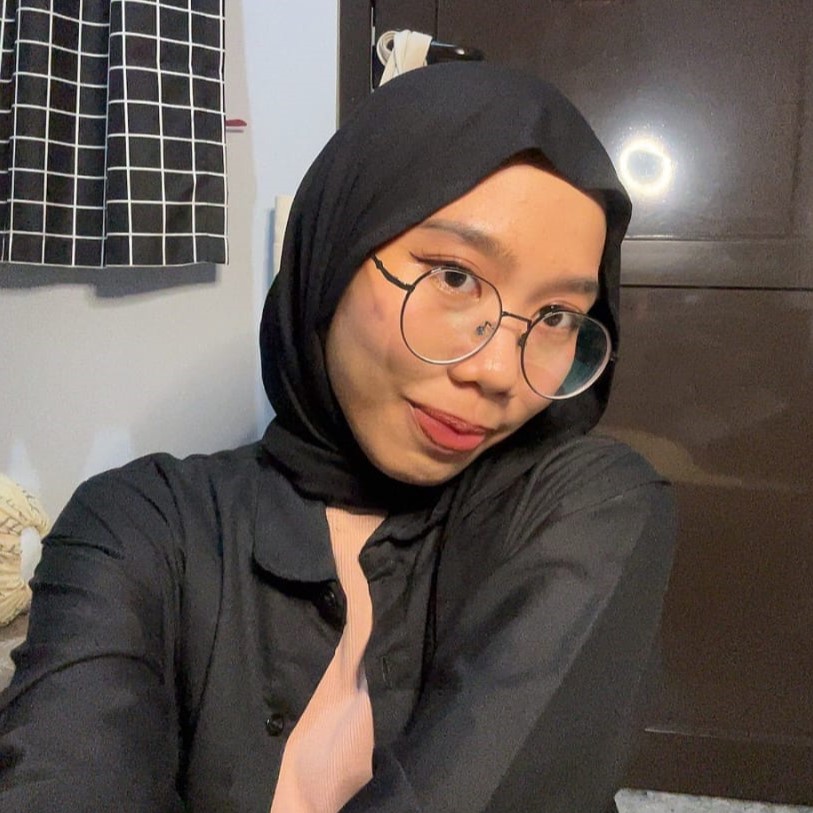
SEO specialist by day, fact-checker by night. An avid reader and content writer dedicated to delivering accurate and engaging articles through research and credible sources.