Enter the world of piping design, where precision and efficiency come together to form interconnected systems with seamless functionality. In this thorough guide, we’ll delve into the details of piping design, offering valuable insights and expert perspectives to enrich your understanding.
What Is Piping Design?
Piping design, a critical component of engineering projects and process plants, is a crucial aspect of creating systems that transport liquids, gases, or solids from one place to another. It involves planning the layout, selecting materials, and determining the connections between pipes, valves, and other components.
In the industry, pipe design is the specialized engineering discipline focused on creating efficient and safe systems for transporting various substances. It plays a vital role in sectors such as oil and gas, power plants, and chemical processing, ensuring the seamless flow of materials while considering factors like safety, efficiency, and compliance with regulations.
What Are The Elements of piping design?
There are three main elements of piping design that determine how a design can be accurate.
2 Dimension or 3 Dimension of piping design
1. Hydraulic Design (flow, velocities, pressure drop)
In pipe design, understanding the hydraulic aspects is crucial. This involves analyzing the flow of fluids, determining velocities within the pipes, and assessing pressure drop to ensure an efficient and effective system.
2. Piping Specification (materials, pipe schedule, rating of elements)
Defining the specifications of the piping system is fundamental. This includes selecting appropriate materials, determining pipe schedules, and assigning ratings to elements, ensuring the system’s compatibility with the intended application.
3. Insulation and Thermal Losses
To address energy efficiency, piping design involves considerations for insulation and thermal losses. This helps in maintaining desired temperatures within the system and minimizing unnecessary energy dissipation.
4. 2D/ 3D Piping Routing and Modeling
Creating detailed plans for the layout is a pivotal step. Utilizing both 2D and 3D models aids in visualizing the entire piping system, ensuring accurate routing, and facilitating effective communication in the design process.
5. Piping Lists
Developing comprehensive lists detailing the various components and specifications within the piping system is essential. This serves as a reference for all involved parties and streamlines the execution of the design.
6. Mechanical Piping Design (thickness calculation) According to ASME B31.1 / B31.3 / EN13480, etc.
Adhering to industry standards such as ASME B31.1, ASME B31.3, or EN13480, mechanical design involves calculating the thickness of pipes. This ensures that the piping system can withstand the internal and external forces it may encounter during operation.
7. Isometric Drawings for Construction
Providing clear and detailed isometric drawings is vital for construction teams. These drawings offer a three-dimensional representation of the piping system, aiding in accurate and efficient implementation.
8. Bill of Materials / Quantities
Developing a comprehensive bill of materials is necessary to keep track of the required components and quantities. This contributes to efficient procurement and construction processes.
9. As-Built Design
Documenting the final state of the piping system, known as the As-Built design, ensures that the constructed system aligns with the original design intent. This documentation serves as a valuable reference for future maintenance and modifications.
Flexibility Analysis
1. Piping Flexibility Analysis According to ASME B31.1/B31.3 / EN 13480
A crucial element is conducting flexibility analysis in accordance with industry standards like ASME B31.1, B31.3, or EN 13480. This involves assessing how pipes respond to thermal expansion or contraction, ensuring that the system can accommodate these changes without causing stress-related issues.
2. Supports Design (type and position)
Determining the type and position of supports is a key aspect of piping design. The proper selection and placement of supports are essential to maintain stability and prevent excessive movements or stresses in the piping system.
3. Buried Pipes
Consideration for pipes that are buried is vital in piping design. Understanding the impact of soil conditions and environmental factors on buried pipes ensures their integrity over time, preventing potential issues like corrosion or deformation.
4. Check of Allowable Loads on Nozzles (pumps, static equipment, etc.) as Per WRC-107
Ensuring that the loads on equipment nozzles, such as those on pumps or static equipment, are within allowable limits is critical. This involves using standards like WRC-107 to assess and verify the structural integrity of these connections.
5. Dynamic analysis (Modal, Harmonic)
Dynamic analysis, encompassing modal and harmonic analyses, is an essential element in piping design. This involves evaluating the system’s response to dynamic forces, such as vibrations or pulsations, ensuring that the piping can withstand these dynamic conditions without compromising its structural integrity.
Advanced Piping Flexibility Analysis
1. Determination of SIF (stress intensification factor)according to B31J for Special geometries not covered by ASME B31.1/B31.3
In advanced piping flexibility analysis, determining the Stress Intensification Factor (SIF) is crucial, especially for unique geometries not covered by standard codes like ASME B31.1/B31.3. This involves using methodologies outlined in B31J to assess and factor in stress intensification in non-conventional piping configurations.
2. Great Diameter or Rectangular Ducts/Pipes When Eigen Buckling Failure Mode Analysis is Required
When dealing with large-diameter pipes or rectangular ducts, Eigen Buckling failure mode analysis becomes necessary in advanced flexibility analysis. This involves evaluating the system’s response to buckling under specific conditions, ensuring structural stability in these unique geometries.
3. Special Transitions Pieces (Rectangular/Circular)
Special transitions between rectangular and circular sections require careful consideration in advanced pipe design. Analyzing stress and deformation in these transition areas ensures smooth and reliable operation of the piping system.
4. Special Supports Design
Designing specialized supports is a key element in advanced piping flexibility analysis. This involves tailoring support structures to unique conditions, considering factors like load distribution and thermal expansion, to ensure the overall stability and integrity of the piping system.
5. Creep Range Design/Operation
Advanced flexibility analysis addresses the creep range, where materials deform over time under sustained loads. Designing for and operating within the creep range ensures the long-term durability and reliability of the piping system.
6. Cyclic Loads and Fatigue Analysis
Considering cyclic loads and conducting fatigue analysis is crucial in advanced pipe design. This involves assessing how the piping system responds to repeated loading and unloading cycles, ensuring that it can withstand these dynamic conditions without experiencing fatigue-related failures over time.
What International Standards Provide Guidelines for piping design?
ASME B31.3 – Process Piping
ASME B31.3 sets guidelines for the design, construction, and inspection of process piping systems. It addresses aspects like materials, pressure design, flexibility analysis, and testing, ensuring the safety and reliability of piping systems in various industries.
API 570 – Piping Inspection Code
API 570 focuses on in-service inspection, evaluation, and testing of piping systems used in the refining and chemical process industries. It outlines criteria for assessing the integrity of existing piping infrastructure, covering aspects such as corrosion, material degradation, and structural integrity.
ISO 14692 – Petroleum and Natural Gas Industries – Glass-Reinforced Plastics (GRP) Piping
ISO 14692 provides guidelines for the design and installation of glass-reinforced plastic piping systems in the petroleum and natural gas industries. It addresses considerations like material selection, design principles, and installation practices for GRP piping in challenging environments.
EN 13480 – Metallic Industrial Piping
EN 13480 specifies the design, construction, and testing requirements for metallic industrial piping systems. It covers aspects such as materials, pressure design, welding procedures, and non-destructive testing, ensuring the integrity and safety of metallic piping used in various industrial applications.
What Are Some FAQs Related to piping design?
1. How Does Piping Design Impact Operational Efficiency?
Piping design directly influences operational efficiency by ensuring the seamless flow of fluids, minimizing energy loss, and optimizing layout for ease of maintenance.
2. What Challenges Do Engineers Commonly Face in Piping Design?
Common challenges include material compatibility, thermal expansion issues, and the need for periodic maintenance. Overcoming these challenges requires a holistic understanding of the system.
3. Is Sustainability A Significant Consideration in Piping Design?
Absolutely. Sustainable design involves using eco-friendly materials, minimizing waste, and adopting energy-efficient solutions, contributing to a greener future.
4. How Crucial is Safety in Piping Design?
Safety is paramount. Integrating safety measures in pipe design is essential to prevent accidents, protect personnel, and safeguard the environment.
5. Can Piping Design Contribute to Cost Savings?
Yes, strategic design can lead to cost savings through optimized layouts, reduced material usage, and enhanced energy efficiency.
6. What Role Does Technology Play in Modern Piping Design?
Technology, such as 3D modeling and simulation tools, has revolutionized the design of piping, enabling engineers to visualize and optimize systems before implementation.
Understanding the design of piping is paramount, given its pivotal role in ensuring the safety and reliability of various industries. Knowledge of international standards and guidelines, such as ASME B31.3 and API 570, becomes the cornerstone for crafting piping systems that stand the test of time.
Embracing these standards not only guarantees the structural integrity of the systems but also safeguards the well-being of personnel and the environment. As industries evolve, the significance of staying abreast of the latest developments in piping design becomes increasingly evident, reinforcing the imperative for a meticulous and standards-driven approach to maintaining safety and efficiency in all piping endeavors.
To enhance your grasp of piping Design, consider joining PetroSync’s ASME B31.3 training. This program offers in-depth insights into process piping, covering everything from design intricacies to testing and maintenance procedures. Engaging in this training equips you with the essential knowledge and skills required to navigate the complexities of pipe design, ensuring compliance with international standards and a comprehensive understanding of building robust and secure piping systems.
PetroSync’s ASME B31.3 training is a valuable opportunity to elevate your expertise and contribute effectively to the safety and efficiency of piping infrastructures across diverse industrial contexts.
Credit header image: iStock
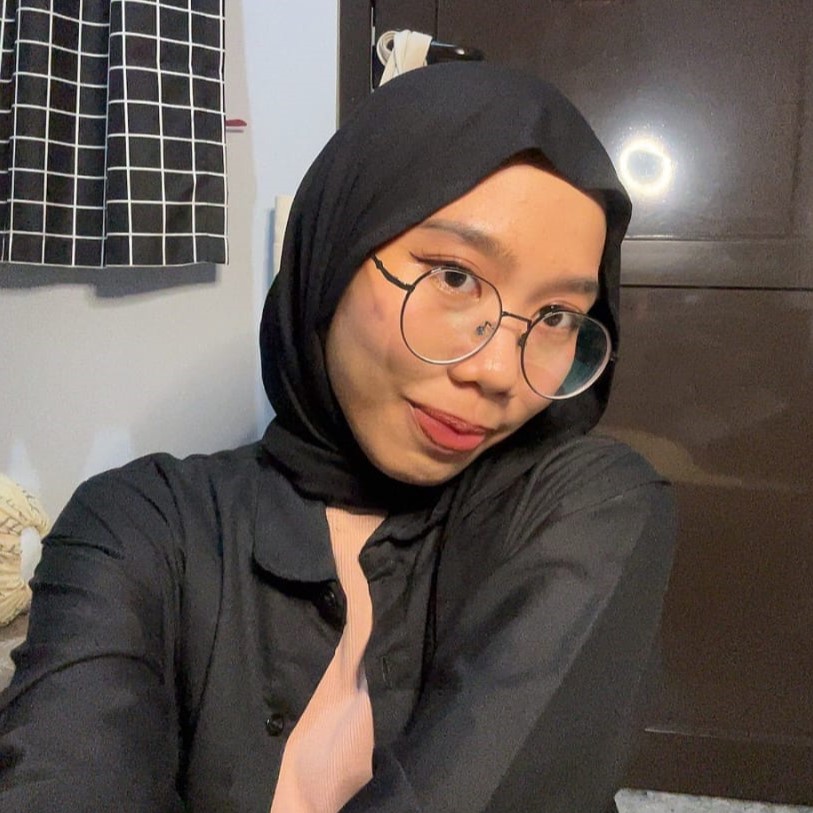
SEO specialist by day, fact-checker by night. An avid reader and content writer dedicated to delivering accurate and engaging articles through research and credible sources.