In this article, we delve into the important concepts of Corrective and Preventive Actions (CAPA) and their vital role in ensuring the reliability and excellence of systems and processes. Discover essential strategies, best practices, and real-world examples illustrating how CAPA contributes to maintaining operational integrity and reducing risks.
What Is Corrective Action (CA)?
Corrective Action (CA) involves a systematic process of identifying, addressing, and rectifying problems or nonconformities in a business or operational setting—a set of actions taken to rectify or change a process that causes errors or nonconforming issues or events. It is a proactive approach aimed at eliminating the root causes of issues, preventing their recurrence, and ensuring continuous improvement.
Corrective Action involves thorough investigation, analysis, and the implementation of effective solutions to enhance overall quality, reliability, and compliance within an organization. This method plays a crucial role in maintaining standards, meeting customer expectations, and fostering a culture of ongoing improvement in processes and products.
What Is Preventive Action (PA)?
Preventive Action (PA) is a proactive and systematic approach taken to identify, anticipate, and eliminate potential issues or sources of errors before they occur in a business or operational process—a system to eliminate any cause(s) that would create a potential hazard or undesirable situation.
The goal of Preventive Action is to prevent the occurrence of problems, reduce risks, and enhance the overall reliability and performance of systems, products, or services. By analyzing historical data, identifying potential risks, and implementing measures to address them,
Preventive Action aims to create a robust and resilient environment that minimizes the likelihood of future errors or non-conformities. This strategy contributes to sustained quality, increased efficiency, and the continual improvement of processes within an organization.
What Is The Difference Between CA and PA?
Corrective Action (CA) and Preventive Action (PA) are two distinct but complementary approaches in quality management. Corrective action involves addressing current issues, such as non-conformities or undesirable situations, by eliminating their root causes to prevent recurrence.
Preventive action, on the other hand, is a proactive strategy focused on averting potential problems before they occur, often informed by risk analysis. It aims to prevent the occurrence of non-conformities, contributing to a robust quality management system and continuous improvement. Both CA and PA play vital roles in ensuring the reliability and excellence of processes within an organization.
What Are Some Examples of A CAPA?
In the oil and gas industry, a corrective and preventive action (CAPA) process is crucial for addressing challenges and ensuring continuous improvement. Here are three examples tailored to specific sectors:
Industry | Issue | Corrective Action | Preventive Action |
Oil and Gas Exploration | During exploratory drilling, unexpected equipment failures result in downtime and increased costs. | Conduct a thorough analysis of equipment failures, implement immediate repairs, and optimize maintenance schedules. | Introduce regular predictive maintenance with advanced monitoring technologies to identify potential issues proactively. |
Petrochemical Manufacturing | Quality control identifies irregularities in the chemical composition of a batch, leading to potential defects. | Halt production, investigate the source of the composition issue, and implement adjustments to correct the current batch. | Enhance quality control protocols, implement additional testing, and update manufacturing processes to prevent similar deviations. |
Renewable Energy Production | In a solar energy facility, a drop in energy output is observed due to the suboptimal performance of certain solar panels. | Assess affected panels, replace or repair malfunctioning components, and restore optimal energy production. | Implement a regular inspection and maintenance schedule for all solar panels, integrating performance monitoring systems for early issue detection. |
What Are The Best Practices When Doing Corrective and Preventive Action?
There are several best practices when doing corrective and preventive action:
1. Proper Definition of Non-Conformance or Risk
The first crucial step in effective Corrective and Preventive Action (CAPA) is to define non-conformances or risks clearly. This involves maintaining a detailed and focused understanding without deviation. The documentation of these issues within a fixed framework provides a solid foundation for the entire CAPA process.
2. Assigning the Right Individuals
Assigning the right people to address non-conformances is paramount. Individuals overseeing the organization’s quality management systems should possess a comprehensive understanding of the organization’s compliance economics. Effective communication about the necessary actions for handling non-conformities is vital for seamless implementation.
3. Standardization in Operational Workflows
Standardization is a key element in avoiding conflicting procedures within operational workflows. The steps taken to address non-conformances should be clear and straightforward, eliminating confusion for organizations and teams involved. Standardizing procedures streamlines the CAPA process, ensuring consistency and effectiveness.
4. Tracking, Reviewing, and Traceability
Enabling tracking, reviewing, and traceability throughout the entire CAPA process is essential. This facilitates analysis to determine the correctness and effectiveness of implemented measures. Implementing a standard monitoring and evaluation mechanism allows organizations to achieve their objectives and proactively mitigate risks associated with non-conformances.
In conclusion, implementing effective Corrective and Preventive Actions (CAPA) is crucial for maintaining reliability in various industries. By properly defining non-conformances or risks, assigning the right individuals, standardizing operational workflows, and ensuring tracking and traceability, organizations can enhance their reliability.
The CAPA process acts as a proactive measure, addressing issues promptly and preventing their recurrence. Ultimately, a well-executed CAPA strategy contributes to sustained reliability, minimizing disruptions and optimizing overall performance in diverse fields.
Join PetroSync Training and Stay Ahead in the Energy Sector
To conclude, Corrective and Preventive Actions (CAPA) play a crucial role in ensuring the reliability of systems and processes. By systematically addressing non-conformities and potential risks, CAPA contributes to the overall dependability of operations.
It serves as a valuable tool in maintaining and enhancing product and process reliability, aligning perfectly with the principles emphasized in the Certified Reliability Engineer (CRE). The inclusion of CAPA in CRE certification underscores its essential role in achieving excellence in reliability engineering.
Mastering CAPA is not just about meeting quality standards; it is about equipping reliability engineers with the skills needed to navigate uncertainties and uphold reliability in various industries.
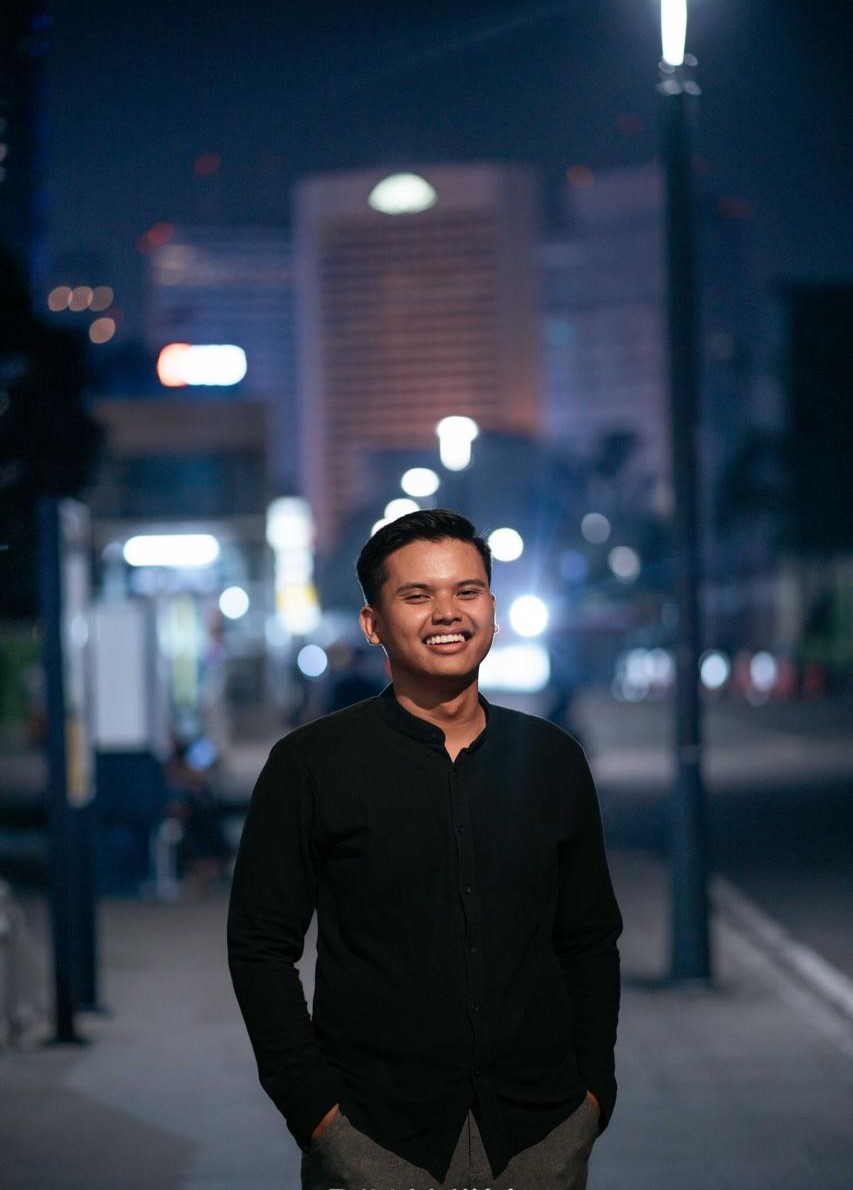
Results-oriented and thorough SEO specialist with extensive experience in conducting keyword research, developing and implementing digital website promotion strategies and plans, managing campaigns to develop company websites in the digital world, excellent knowledge of marketing techniques and principles, and attentive strong attention to detail.