In the dynamic realm of maintenance strategies, Reliability-Centered Maintenance (RCM) Methodology stands out as a cornerstone for optimizing asset performance. This article delves into the intricacies of Function and Functional Failure Analysis within RCM, getting into details on its significance and applications.
What Is Function?
In Functional Failure Analysis, a “function” refers to a description of what a piece of equipment is intended to do, the expected level of performance, and a specific task or purpose that a system, equipment, or process is designed to perform. It is what the component or system is supposed to do.
When conducting this analysis, experts look at the functions of each part and assess how they may be compromised or fail to operate as intended. Understanding functions is crucial because it helps identify potential issues, determine the impact of failures, and implement strategies to prevent or mitigate problems. In essence, functions serve as the building blocks for evaluating the performance and reliability of the overall system.
What Is Functional Failure Analysis?
Functional Failure Analysis examines and helps you understand how a system, equipment, or process may fail to perform at its peak. This analysis looks at what a piece of equipment is supposed to do, the expected level of performance, and identifies functional failures—detailing all the conditions that prevent the equipment from operating at peak performance.
By examining functions and potential failures, organizations can make informed decisions to improve efficiency, reduce downtime, and ensure smooth operations. It is a systematic way to understand and address any shortcomings in how equipment or systems function.
What Is An Example of A Functional Failure?
An example of a functional failure in the oil and gas industry could be a pump that fails to maintain the required pressure levels during the extraction process, akin to a machine that won’t turn on or run at all. In this case, the function of the pump is to ensure the proper flow of oil or gas, and if it fails to do so, it can disrupt the entire extraction operation.
This type of failure might be caused by mechanical malfunctions, insufficient maintenance, or sudden changes in operating conditions. Identifying and addressing such functional failures is crucial to maintaining the efficiency and reliability of operations in the oil and gas industry.
What Are The Types of Functional Failure Analysis?
1. Total Functional Failure
This occurs when a system or component completely ceases to perform its intended function. In other words, the entire functionality of the system is compromised, leading to a complete shutdown or inability to deliver the expected output.
2. Partial Functional Failure
Unlike total functional failure, a partial functional failure involves a degradation in the performance of a system or component. While the system may still operate to some extent, it falls short of delivering its full intended functionality. This could result in reduced efficiency, slower operation, or a decline in the quality of output.
Total Functional Failure | Partial Functional Failure | |
Definition | Complete cessation of a system or component’s intended function. | Degradation in the performance of a system or component. |
Example |
|
|
Type of Required Maintenance | Typically involves corrective maintenance to restore the system to its normal functionality. | Involves preventive or corrective maintenance to address the specific issue causing the partial failure. |
How To Create Functional Failure Analysis?
To create a Functional Failure Analysis (FFA), you need to follow a systematic process to examine and understand potential failures within a system. Here’s a step-by-step guide:
1. Select an Item
To initiate a Functional Failure Analysis, start by navigating to the system hierarchy and selecting the relevant item. Once identified, choose “Analysis > FMEA > Add FMEA” to create a dedicated space for the analysis.
2. Choose a View
Upon entering the Analysis panel, you are presented with various views. Opt for the Hierarchy view to visualize analysis records in a hierarchical tree structure, providing a broad overview. Alternatively, use the Worksheet view for a tabular format or the Filtered view to focus on specific record types. Select the most suitable view based on your preference and the complexity of the analysis.
3. Describe Functions
You should articulate the functions the equipment is intended to perform in the chosen view, likely the Worksheet view. This step involves a detailed description of the expected tasks or purposes of the system, outlining its primary functions within the context of the analysis.
4. Describe Potential Functional Failures
Continuing within the chosen view, elaborate on potential functional failures. Identify and document instances where the equipment may fall short in performing its intended functions. This step serves as an anticipatory measure to understand vulnerabilities within the system.
5. Describe the Effects of Each Functional Failure
Proceed to describe the effects of each identified functional failure. Examine and articulate the consequences or impacts that each failure might have on the overall system. This step provides insights into the severity and significance of potential issues.
6. Describe Potential Failure Modes
Concluding the analysis within the selected view, describe the potential failure modes. This involves specifying the various ways in which the equipment might fail in performing its functions. By elucidating potential failure modes, you gain a comprehensive understanding of 7. the risks associated with the system.
By meticulously following these steps and utilizing the available views, you systematically undertake a Functional Failure Analysis. This structured approach ensures a thorough examination of the system’s functionality, potential failure points, and their corresponding effects, aiding in the development of effective strategies for maintenance and risk mitigation.
Join the Best – PetroSync Training for Oil & Gas Professionals
Reliability engineers actively use Functional Failure Analysis (FFA) as an integral part of the Reliability Centered Maintenance (RCM) methodology to enhance their performance. As a reliability engineer, you understand the significance of identifying and mitigating potential failures in complex systems. FFA within the RCM framework equips you with the means to systematically analyze functions, failures, and their consequences, allowing for strategic decision-making in maintenance planning.
Now, imagine the impact of elevating your skills further through comprehensive RCM training. By joining the RCM training by PetroSync, you’ll gain in-depth insights into the principles and practices of Reliability Centered Maintenance, including hands-on experience with tools like Functional Failure Analysis.
The RCM training will empower you to navigate the intricacies of asset management with precision, helping you optimize maintenance strategies, minimize downtime, and contribute significantly to the reliability and success of your organization’s critical systems.
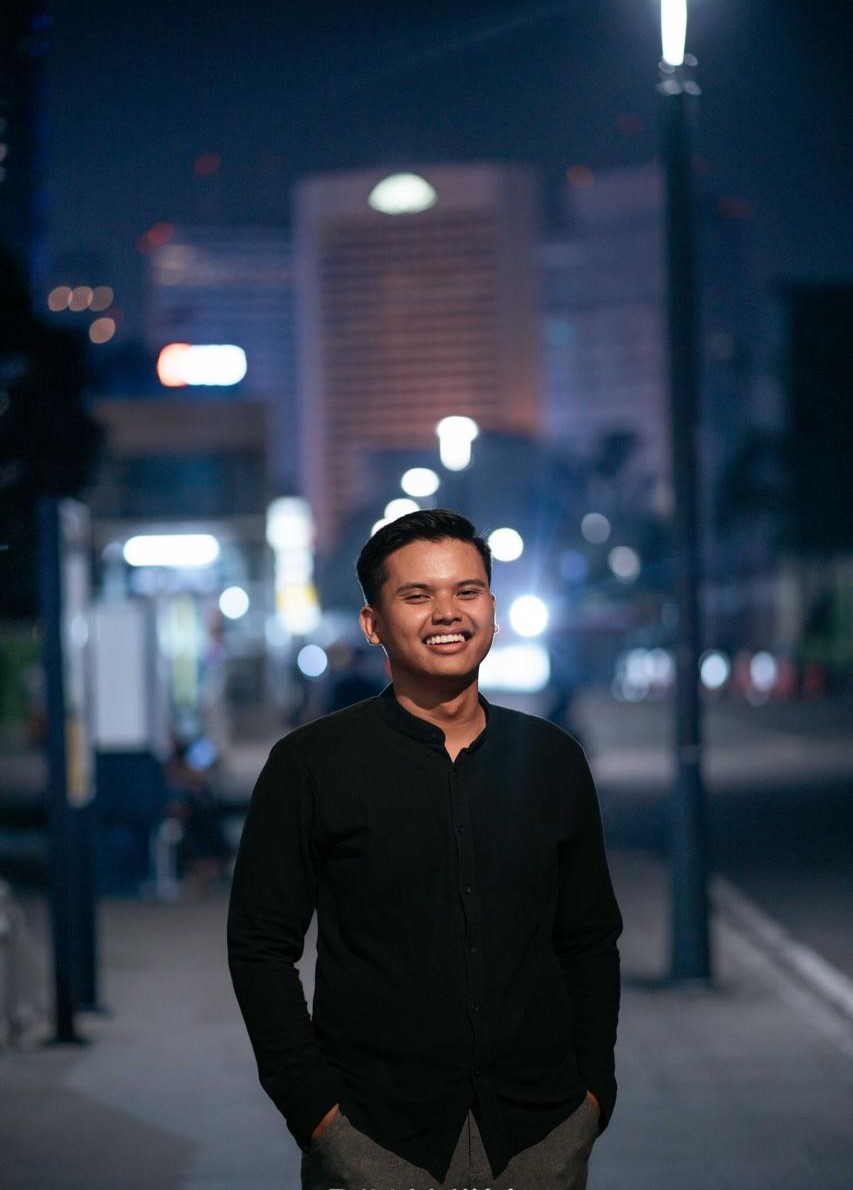
Results-oriented and thorough SEO specialist with extensive experience in conducting keyword research, developing and implementing digital website promotion strategies and plans, managing campaigns to develop company websites in the digital world, excellent knowledge of marketing techniques and principles, and attentive strong attention to detail.