In the asset management field, it’s vital to grasp the full scope of expenses related to an asset for informed decision-making and planning. Life cycle costing is a key concept that takes a comprehensive view of all costs an asset will incur throughout its entire lifespan. Instead of just considering the initial purchase costs, life cycle costing examines ongoing operating expenses, periodic replacements, modifications, and the eventual disposal or salvage value.
What Is Life Cycle Costing Analysis?
Life cycle costing analysis is a comprehensive approach to evaluating the total costs associated with an asset throughout its entire lifespan. It goes beyond initial purchase or installation expenses and considers all expenses incurred over the asset’s life, including operation, maintenance, and disposal costs.
The analysis is a key asset management tool that takes into account the whole life implications of planning, acquiring, operating, maintaining, and disposing of an asset. The process is an evaluation method that considers all ownership and management costs.
In accounting, life cycle costing involves gathering all the expenses an asset will generate throughout its existence. This encompasses the initial investment, future additional investments, recurring annual costs, and disposal expenses.
Efficiently managing an asset’s life cycle enhances its longevity and functionality. Collecting information about assets provides insights into their current status in the life cycle, improving overall system efficiency and the level of service.
Why Is Life Cycle Costing Analysis Important in Asset Management?
Life cycle costing Analysis holds significant importance in asset management because it enables a comprehensive consideration of all costs associated with an asset throughout its entire life.
Unlike focusing solely on immediate purchase costs, life cycle costing emphasizes holistic, long-term expenses, including operation, maintenance, repair, monitoring, and rehabilitation costs. Neglecting operational expenses while concentrating only on capital expenses limits an organization’s ability to optimize its life cycle costs.
Without proper attention to life cycle costing, a system might face unexpected challenges, such as higher-than-anticipated replacement costs, additional training needs, or increased staffing requirements. This approach ensures a thorough understanding of expenses and aids in making informed decisions for efficient and cost-effective asset management.
What Factors Are Considered in Life Cycle Costing Calculations?
In life cycle costing calculations, various elements are taken into consideration to provide a comprehensive analysis of the overall costs associated with an asset. These elements include:
1. Initial Capital Cost
This involves the upfront expenses associated with acquiring the asset, covering purchase, installation, and any other initial costs.
2. Annual Operating Cost
This factor considers the ongoing costs related to the asset’s operation, including expenses for energy consumption and regular maintenance.
3. Periodic Replacements
Over the asset’s lifespan, certain components may need replacement or refurbishment at scheduled intervals, and these costs are factored into the life cycle analysis.
4. Additions and Alterations
Any modifications or upgrades made to the asset during its service life are included in the analysis.
5. Use Costs
These encompass expenses directly related to utilizing the asset, such as training, monitoring, or any additional costs incurred during regular operation.
6. Salvage Value
The potential value that can be recovered from the asset at the end of its useful life, either through resale or recycling.
The culmination of life cycle costing analysis typically results in a single-number figure representing either the present value or equivalent annual value of all anticipated costs throughout the economic life of the asset.
How To Do Life Cycle Cost Analysis?
Conducting a Life Cycle Cost Analysis involves following a structured process within the framework of traditional design or problem-solving. Here’s a step-by-step guide
1. Define Objectives
Clearly outline the objectives of the life cycle cost analysis. Understand what you aim to achieve and consider the specific aspects you want to evaluate over the asset’s lifespan.
2. Identify Alternatives
Explore different alternatives related to the asset, considering various options that may influence its life cycle costs. This could include variations in design, technology, materials, or maintenance approaches.
3. Define Assumptions
Establish the assumptions that will be used as the basis for your analysis. These assumptions could relate to factors like asset lifespan, maintenance requirements, operational conditions, and economic considerations.
4. Project Benefits and Costs
Estimate both the benefits and costs associated with each alternative. Consider the initial investment, operational expenses, maintenance costs, potential benefits, and any other relevant financial factors.
5. Evaluate Alternatives
Assess the life-cycle cost of each alternative based on the projected benefits and costs. This step involves a comprehensive review of the financial implications and impacts of each option.
6. Decide Among Alternatives
Utilize the life cycle cost estimates as one of the factors in the decision-making process. Evaluate all alternatives against your defined objectives and make informed decisions considering the holistic view of costs over the asset’s life.
By following these steps, organizations can systematically analyze and compare different alternatives, helping them make informed decisions that align with their objectives and result in optimal life cycle cost management.
In the field of asset management, life cycle cost analysis plays a vital role by offering a comprehensive view of an asset’s economic impact. The analysis goes beyond immediate purchase considerations, providing a strategic perspective to optimize short-term spending and enhance long-term asset value. Essentially, it empowers decision-makers to navigate the complexities of asset management, ensuring efficiency, cost-effectiveness, and the achievement of long-term goals.
Join PetroSync Training to Transform Your Professional Path
As you recognize the significance of life cycle cost analysis, consider furthering your expertise by participating in ISO 55000 training offered by PetroSync. This specialized training provides a unique opportunity to gain hands-on knowledge and practical insights into implementing asset management best practices, including the principles of ISO 55000. Equip yourself with the skills needed to navigate the complex landscape of asset management effectively.
Joining this training will not only enhance your understanding of ISO 55000 but also empower you to contribute significantly to optimizing asset performance and achieving organizational goals. Elevate your expertise and make a valuable impact by enrolling in ISO 55000 training by PetroSync!
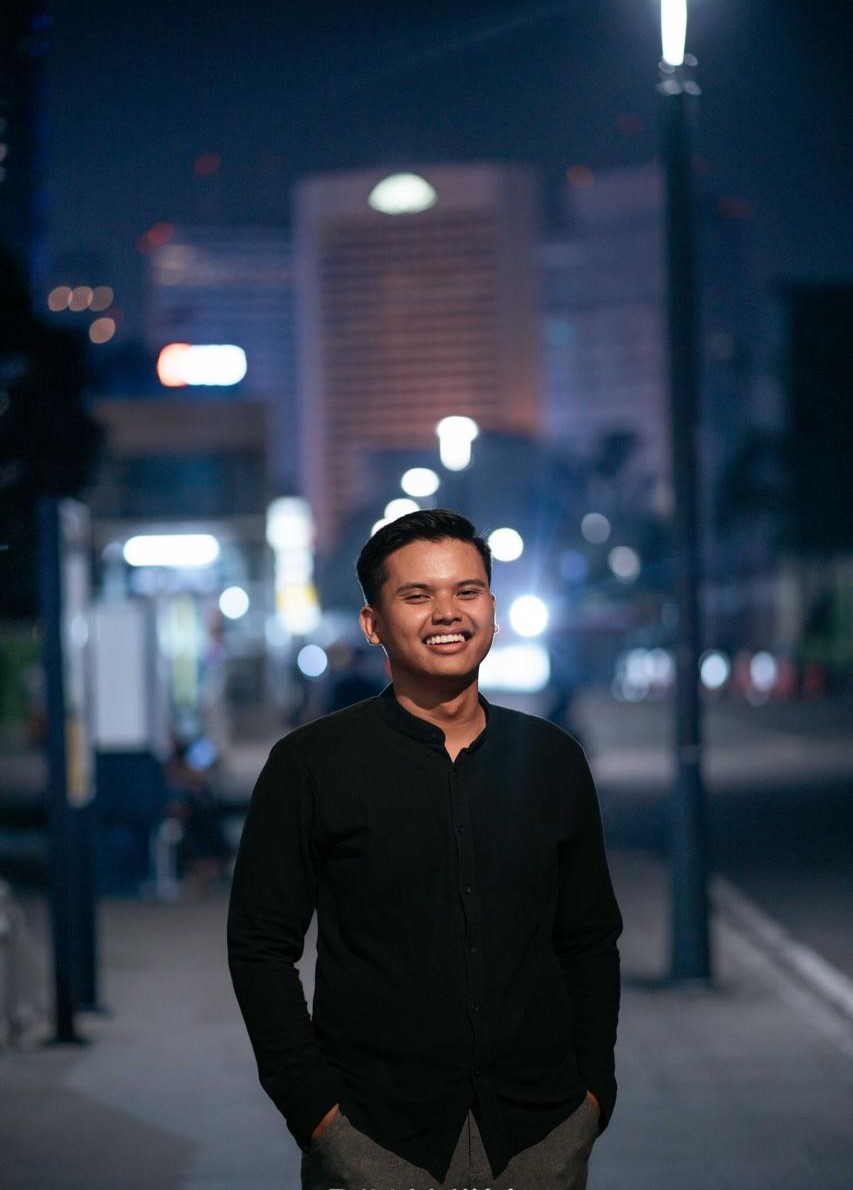
Results-oriented and thorough SEO specialist with extensive experience in conducting keyword research, developing and implementing digital website promotion strategies and plans, managing campaigns to develop company websites in the digital world, excellent knowledge of marketing techniques and principles, and attentive strong attention to detail.