In industries the place of each 2d of downtime translates to substantial losses, making sure constant tools overall performance is now not simply a technical aim – it’s an enterprise imperative. This is specially actual in sectors like oil and gas, the place where asset failure can disrupt complete operations and incur tens of millions in unplanned costs.
As organizations push for greater efficiency, decrease risk, and extra sustainable operations, Maintenance Reliability Engineering (MRE) has emerged as a core pillar in attaining height uptime. But what exactly does MRE entail? How is it different from traditional maintenance? And how can professionals apply its principles to unlock real-world performance improvements? Let’s dive deeper.
What is Maintenance Reliability Engineering?
Maintenance Reliability Engineering refers to the systematic utility of engineering principles, statistics analysis, and asset administration techniques to beautify the overall performance and dependability of bodily systems. The fundamental intention is to extend Mean Time Between Failures (MTBF) whilst lowering unplanned downtime and preservation costs.
Unlike usual maintenance, which frequently reacts to troubles after they occur, MRE is grounded in proactive and predictive approaches. Techniques such as Root Cause Analysis (RCA), Failure Modes and Effects Analysis (FMEA), and Reliability Centered Maintenance (RCM) are central to this discipline.
These methodologies no longer solely assist perceived failure factors however additionally allow engineers to construct techniques that stop recurrence. According to a McKinsey report, effective reliability centered strategies can reduce maintenance costs by up to 20% and increase asset availability by 10–20% across heavy industries.
What is Reliability in Engineering?
Reliability, in the engineering context, refers to the chance that a device or factor performs its supposed characteristic except failure below distinct prerequisites for a unique duration of time. In easy terms: it’s about consistency and dependability. High‑reliability systems are not just well‑designed; they’re also well‑maintained and continuously optimized. Reliability considers various factors, including:
- Design integrity
- Operational environment
- Maintenance quality
- Human error mitigation
By focusing on these variables, groups can lengthen asset existence cycles and obtain safer, greater environment friendly operations. In industries like oil and gas, the place protection and compliance are paramount, reliability engineering isn’t optional – it’s essential.
What is the Difference Between Maintenance and Reliability Engineer?
While their roles are closely related, maintenance engineers and reliability engineers have distinct focuses:
- Maintenance Engineers are accountable for the everyday preservation of equipment. They make certain machines jog and troubleshoot problems as they arise.
- Reliability Engineers on the other hand, take a broader view. Their center of attention is long‑term: figuring out patterns, getting rid of root motives of failures, and growing structures to forestall breakdowns altogether.
Reliability engineers regularly work cross‑functionally, participating with operations, safety, and manufacturing groups to align reliability efforts with enterprise goals. They remember closely on facts analytics, situation monitoring, and reliability modeling.
In mature organizations, these roles complement every other. Maintenance engineers manage on the spot needs, whilst reliability engineers construct sustainable strategies.
How Do You Calculate Maintenance Reliability?
Quantifying reliability involves several key metrics, the most common being:
- Mean Time Between Failures (MTBF): Measures the average time between equipment failures. A higher MTBF indicates greater reliability.
- Mean Time To Repair (MTTR): Indicates how quickly equipment can be restored to operation after failure.
- Failure Rate (λ): Often used in probabilistic models, calculated as 1/MTBF.
Formula: MTBF = Total Operating Time ÷ Number of Failures
These metrics are necessary for predictive protection techniques and lifecycle fee analysis. By always monitoring and optimizing these indicators, reliability engineers can show ROI for their efforts and attain government buy-in.
What is the Process of Reliability Engineering?
Implementing reliability engineering within an organization involves a structured process:
1. Asset Criticality Analysis – Prioritize equipment based on failure consequences and business impact.
2. Failure Mode Analysis (FMEA) – Identify all possible failure modes and their effects.
3. Root Cause Analysis (RCA) – Investigate the underlying reasons for recurring failures.
4. Strategy Development – Define preventive, predictive, and corrective maintenance actions.
5. Implementation – Deploy solutions, train staff, and integrate into operations.
6. Continuous Monitoring – Use KPIs, sensors, and inspections to assess progress.
When performed right, this strategy transforms reliability from a reactive characteristic into a strategic commercial enterprise enabler. It builds a subculture of accountability, cross‑team collaboration, and data‑driven decision‑making.
According to a lookup posted in Emerald Insight, companies that enforce a structured reliability application can limit tools downtime by up to 40% and enhance asset utilization charges significantly.
Your Gateway to Industry Excellence: Join PetroSync Training
In today’s asset‑driven industries, reliability engineering performs a pivotal position in decreasing downtime and maximizing operational efficiency. However, actual mastery in this area needs greater than on‑the‑job experience—it requires structured insights, world fantastic practices, and verified equipment that flip preservation into a few drivers.
That’s precisely what PetroSync delivers. Our coaching packages are tailor-made for authorities who lead or impact reliability strategies, supplying deep, realistic appreciation of standards like RCM, MTBF, FMEA, and ISO 55000—all guided by means of specialists with real‑world enterprise experience.
PetroSync has empowered lots of engineers, managers, and executives throughout the oil & gasoline and manufacturing sectors to put into effect options that end result in tangible overall performance gains—often boosting uptime by means of 15–30%.
Whether you are aiming to streamline your renovation strategy, decrease tools failures, or construct a proactive reliability culture, PetroSync presents the equipment and insights you need. With education handy in Jakarta, Kuala Lumpur, Dubai, and online, we make it effortless for gurus like you to make investments in long‑term operational excellence.
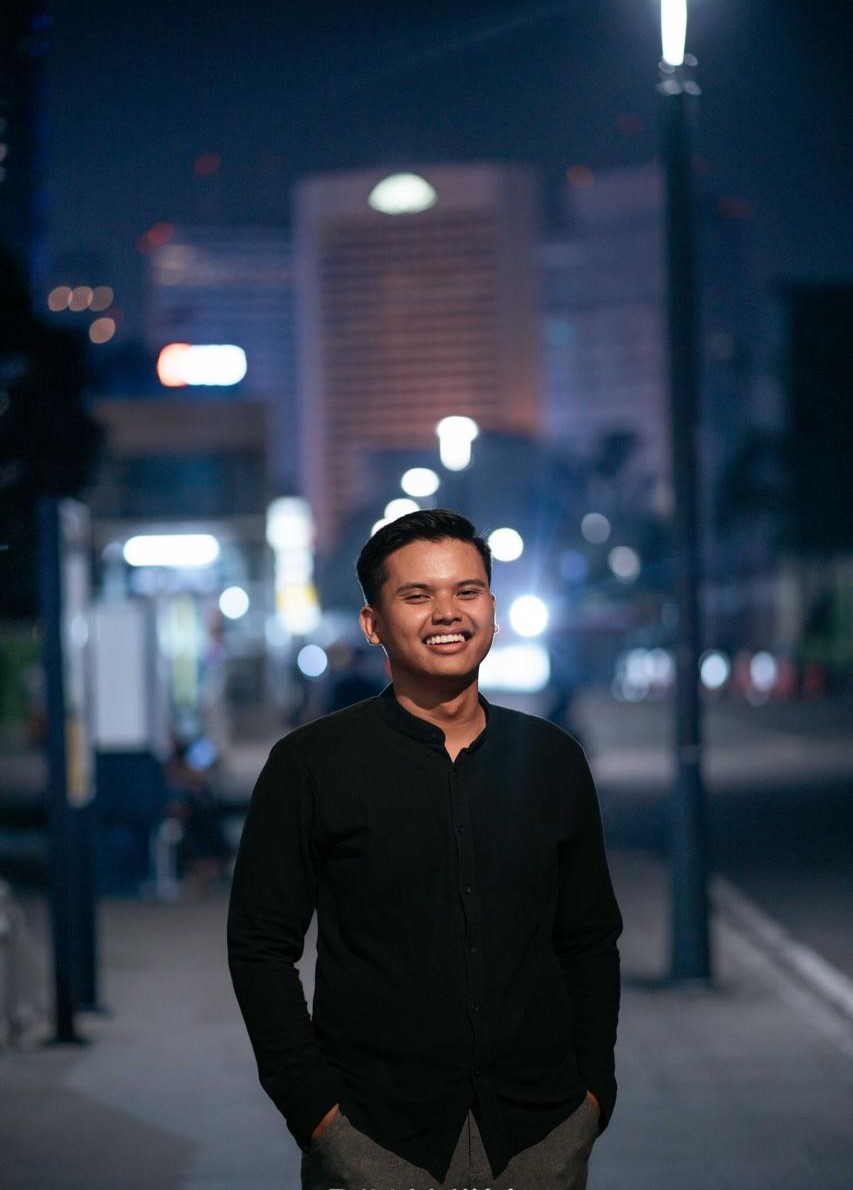
Results-oriented and thorough SEO specialist with extensive experience in conducting keyword research, developing and implementing digital website promotion strategies and plans, managing campaigns to develop company websites in the digital world, excellent knowledge of marketing techniques and principles, and attentive strong attention to detail.