Pipeline inspection is a crucial process that ensures the safety, reliability, and effectiveness of pipelines that span vast distances, carrying various substances like oil, gas, water, and chemicals. As these pipelines play a significant role in our modern infrastructure, it becomes essential to regularly inspect them for potential defects. This article explores the world of pipeline inspection, discussing the methods, technologies, and standards used to assess and maintain pipelines.
What Is a Pipeline Inspection?
Pipeline inspection is an integral component of pipeline integrity management to ensure its optimal condition. Pipeline safety regulations like API 570 govern these inspection activities. In most companies, it is customary for their pipelines to undergo regular inspections.
When inspecting pipelines, the process involves examining and assessing the condition, strength, and performance of pipelines utilized for various purposes, such as transporting fluids like oil, gas, and water. This inspection encompasses underground and aboveground pipelines to verify their proper functionality and adherence to safety standards and to detect potential issues or damages.
How Does The Pipeline Inspection Procedure Work?
During pipeline inspections, specialized equipment and techniques evaluate factors like structural integrity, corrosion levels, leaks, and overall pipeline health. These inspections are of utmost importance as they help identify any flaws, weaknesses, or susceptibilities that could lead to pipeline failures.
Various pipeline inspection procedures are designed to assess the performance capacity of pipelines. These procedures include:
Step 1: Visual Inspection
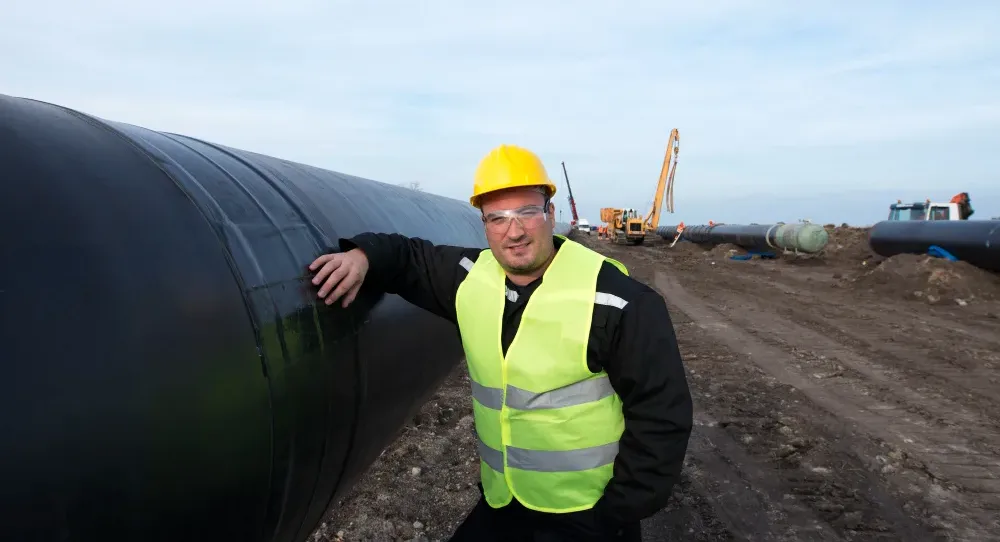
Visual inspection in pipeline inspection involves directly examining the pipeline using human visual senses or optical devices. Piping inspectors visually assess the external surface and accessible internal components for visible defects, anomalies, or signs of damage. This is the initial step in pipeline inspection to determine the need for further testing or maintenance actions.
Step 2: Non-Destructive Testing (NDT)
Non-destructive testing (NDT) is conducted as the second step in pipeline inspection to complement and enhance the findings from visual inspection. While visual inspection is valuable, it may not comprehensively assess the pipeline’s internal condition. Common NDT methods encompass:
a. Ultrasonic Testing
Ultrasonic testing is performed on pipelines to assess any issues like cracks, corrosion, or changes in wall thickness. The testing uses equipment emitting high-frequency sound waves into the pipeline and analyzes the waves that bounce back as a sign of issues.
The equipment receives the reflected waves and then converts them into electrical signals. These signals are then analyzed to determine if there are any defects or abnormalities in the pipeline.
b. Magnetic Particle Testing
Magnetic particle inspection is a method of inspecting ferromagnetic materials to detect surface defects by passing an electrical current through them. It can also identify defects located slightly below the material’s surface.
This method is particularly effective in identifying flaws like cracks and weld discontinuities that could compromise the material’s integrity. Magnetic Particle Testing can be performed using different techniques, including direct contact, wet suspension, or dry powder methods, depending on the material being inspected and the type of defect being sought.
c. Radiographic Testing
Radiographic Testing (RT) is a non-destructive inspection technique that utilizes either x-rays or gamma rays to analyze the inner composition of manufactured parts and detect any imperfections or faults present.
In Radiographic Testing, a radiographic source, such as an X-ray machine or a radioactive isotope, is positioned on one side of the material. The radiation passes through the material and interacts differently with areas of varying thickness or density.
On the opposite side, a radiographic film or digital detector captures the transmitted radiation. The resulting radiographic image shows the material’s internal structure, highlighting density differences like voids, cracks, weld defects, or inclusions.
d. Eddy Current Testing
Eddy Current Testing is a method that utilizes electromagnetic induction to detect defects in pipelines and tubing. A probe is inserted into the tube and moves along its entire length. The electrical impedance is measured by generating eddy currents through the electromagnetic coils within the probe to monitor any changes.
By studying these changes, Eddy Current Testing can identify and assess various flaws, including surface cracks, pitting, material thickness variations, and conductivity changes. This technique is sensitive, efficient, and applicable to various conductive materials, making it valuable in aerospace, automotive, manufacturing, and power generation.
e. Hydrostatic Testing
Hydrostatic testing is used to evaluate the strength and detect leaks in pipelines. The testing involves filling the equipment with water, ensuring no air pockets, and applying a predetermined pressure level for a specific duration.
During hydrostatic testing, the equipment is carefully filled with water to ensure complete saturation. The water is pressurized above the normal operating level, often exceeding 1.5 times the standard pressure. This elevated pressure is maintained for a designated time, usually, several minutes or hours, while closely monitoring for any pressure drops or signs of leaks.
The main objective of hydrostatic testing is to verify that the equipment can withstand the intended operating pressure without significant leaks or deformations.
f. Charpy Impact Testing
Charpy Impact Testing is a standardized method to assess materials’ toughness and impact resistance, particularly metals. This testing helps determine the material’s ability to withstand sudden loads or impacts and absorb energy without fracturing or breaking.
g. Magnetic Flux Leakage
Magnetic Flux Leakage (MFL) is a non-destructive testing method utilized to examine the condition of ferromagnetic materials like pipelines. It involves creating a strong magnetic field within the material and detecting any leakage of magnetic flux caused by defects or abnormalities.
During Magnetic Flux Leakage testing, a highly magnetized probe or sensor is moved along the surface of the material being inspected. As the magnetic field interacts with the material, it follows the path of least resistance. If there are any irregularities such as cracks, corrosion, or material loss, the magnetic field will leak or divert, resulting in noticeable flux leakage.
h. Guided Wave Testing
Guided Wave Testing (GWT) is a method of non-destructive testing used to examine lengthy structures like pipelines for hidden defects. It sends low-frequency mechanical waves along the structure, guided by its shape, to detect and locate potential problems.
During Guided Wave Testing, a transducer is placed on the structure’s outer surface to generate mechanical waves that travel along its length, interacting with any defects and producing reflections. These reflections are then analyzed to identify the location, severity, and type of issues, such as corrosion, thinning, or cracks.
Step 3: In-line Inspection (ILI) or “Smart Pigging”
While NDT methods provide valuable information about the pipeline’s internal condition, they have limitations regarding coverage and accessibility. In contrast, ILI involves using advanced devices called smart pigs that travel through the pipeline, collecting data on parameters like wall thickness, corrosion levels, and internal characteristics along the entire length. Smart pigs are equipped with sensors and instruments that detect defects, measure wall thickness, and identify corrosion.
Step 4: Leak Detection Systems
Once ILI is completed, leak detection systems are employed to specifically locate and identify any potential leaks or breaches in the pipeline. These systems utilize various technologies such as pressure sensors, acoustic sensors, or flow meters to monitor the pipeline for any indications of leakage continuously.
Step 5: Pressure Testing
Pressure testing is performed after implementing a leak detection system in pipeline inspections to verify the pipeline’s strength and integrity under normal operating conditions.
After installing the leak detection system, pressure testing assesses how well the pipeline can withstand the intended operating pressure without significant issues.
The pipeline is subjected to higher pressure levels during pressure testing than its normal operating pressure. This elevated pressure allows for a thorough evaluation of the pipeline’s performance, simulating real-world conditions and ensuring its ability to handle the expected flow of fluids or gasses safely.
Step 6: Cathodic Protection Inspection
Cathodic protection inspection is performed after pressure testing in pipeline inspections to evaluate and uphold the effectiveness of the cathodic protection system in preventing corrosion.
After completing the pressure testing, cathodic protection inspection focuses on safeguarding against corrosion.
Cathodic protection involves using a direct current to counteract the electrochemical reactions that cause deterioration. Conducting cathodic protection inspection following pressure testing ensures that the pipeline’s corrosion prevention measures function properly. This inspection entails assessing the system’s efficacy, measuring electrical potentials, and visually inspecting the anodes or impressed current sources.
Why Is A Pipeline Inspection Necessary?
When conducting a pipeline inspection, it is essential to consider various factors to ensure a comprehensive assessment of the pipeline’s condition and performance. These factors include:
1. Structural Integrity
It is necessary to evaluate the overall structural integrity of the pipeline to identify any deformations, corrosion, or mechanical damage that may affect its strength and stability.
2. Leakage Detection
Detecting leaks or signs of fluid seepage along the pipeline is crucial to prevent environmental contamination, minimize losses, and ensure safe transportation.
3. Corrosion Assessment
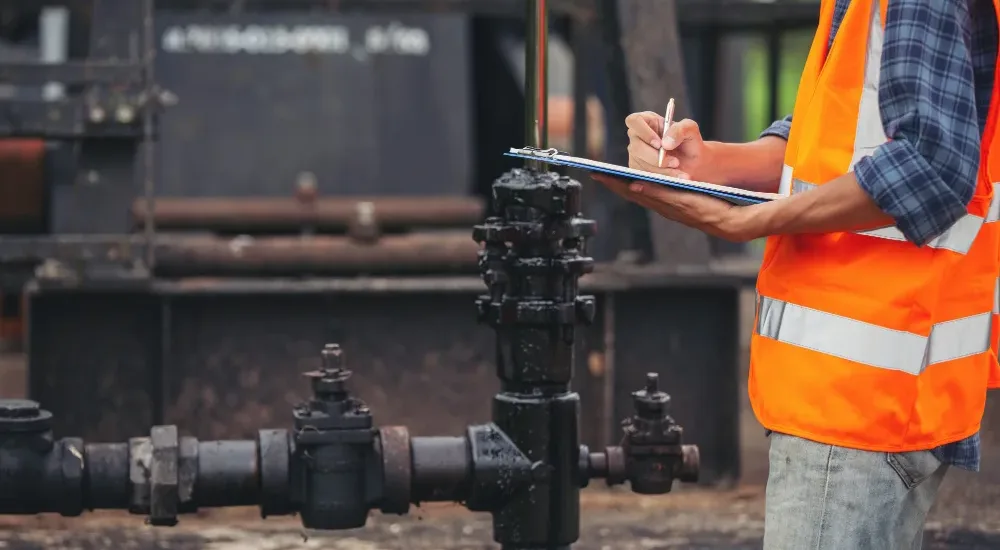
Assessing the level of corrosion on the pipeline’s surfaces is important as corrosion can weaken the material over time and increase the risk of failures or ruptures. Techniques like ultrasonic testing or electromagnetic inspection may be used.
4. Operational Performance
The inspection should evaluate the pipeline’s operational performance, including flow rate, pressure levels, and temperature control, to ensure it is functioning properly.
5. Coating and Insulation Evaluation
The condition of the pipeline’s coating and insulation systems should be assessed to determine if they protect the pipeline from external environmental factors such as moisture or corrosion.
6. Geotechnical Considerations
For underground pipelines, evaluating the surrounding soil conditions, potential ground movement, and other external factors that could impact the pipeline’s stability and integrity is essential.
7. Compliance with Regulations
The inspection process should verify whether the pipeline complies with relevant safety standards, regulations, and codes, ensuring adherence to industry and governmental requirements.
8. Maintenance and Repair Need
Identifying areas that require maintenance or repair is critical to address potential issues promptly and mitigate risks. This involves identifying areas with compromised integrity, vulnerable joints, or damaged components.
9. Data Analysis and Reporting
The collected inspection data should be carefully analyzed, interpreted, and documented to generate a comprehensive report highlighting the pipeline’s condition, identifying concerns, and recommending appropriate actions or maintenance strategies.
What Are The Benefits of Doing Pipeline Inspections?
Pipeline inspections offer numerous advantages and benefits. They are essential for ensuring pipeline systems’ safety, reliability, and efficiency. In general, regular pipeline inspection has seven benefits:
1. Improved Safety
Inspections identify potential hazards, defects, or weaknesses in pipelines, promoting overall safety and minimizing the risk of accidents, leaks, or harm to people and the environment.
2. Early Issue Detection
Early on, inspections catch pipeline defects, such as corrosion, cracks, or mechanical failures. Inspectors enable proactive maintenance by addressing these problems promptly, reducing the likelihood of costly repairs or sudden failures.
3. Regulatory Compliance
Inspections ensure adherence to safety and environmental regulations, demonstrating compliance and avoiding potential penalties or legal repercussions.
4. Optimal Performance
Inspections assess flow capacity, pressure levels, and structural integrity, ensuring pipelines operate efficiently and effectively.
5. Cost Savings
Regular inspections lead to long-term cost savings. By addressing minor issues promptly, inspections prevent more significant and expensive repairs. They also optimize maintenance schedules, reducing downtime and extending the pipeline system’s lifespan.
6. Environmental Protection
Inspections detect and address leaks or potential sources of pollution, safeguarding the environment and preventing spills or contamination.
7. Stakeholder Confidence
Routine inspections demonstrate a commitment to safety, reliability, and responsible operation, instilling confidence in communities, regulators, investors, and customers.
Pipeline inspections offer enhanced safety, early issue detection, regulatory compliance, optimal performance, cost savings, environmental protection, and stakeholder confidence. They are proactive measures to uphold pipeline integrity, ensuring smooth and secure fluid or gas transportation.
In conclusion, conducting proper pipeline inspections is crucial for piping inspectors. It is a vital duty that ensure the integrity, safety, and effectiveness of pipeline systems. Through meticulous inspections, potential flaws and risks can be identified, enabling timely repairs and upkeep.
API, as the leading inspection association, comes up with API 570 Piping Inspector certification to be an international benchmark assessing the competence and proficiency of piping inspectors. This esteemed certification establishes a comprehensive framework for evaluating the necessary knowledge and skills needed to effectively evaluate the integrity of piping systems.
By enrolling in the PetroSync‘s API 570 Piping Inspector training course, you can enhance your preparation for obtaining the API 570 certification. This comprehensive training program equips you with the necessary knowledge and skills required to excel in the field of piping inspection. Enroll in API 570 training and take a proactive step towards advancing your career and becoming a highly competent and sought-after piping inspector with PetroSync!
Credit header image: Freepik
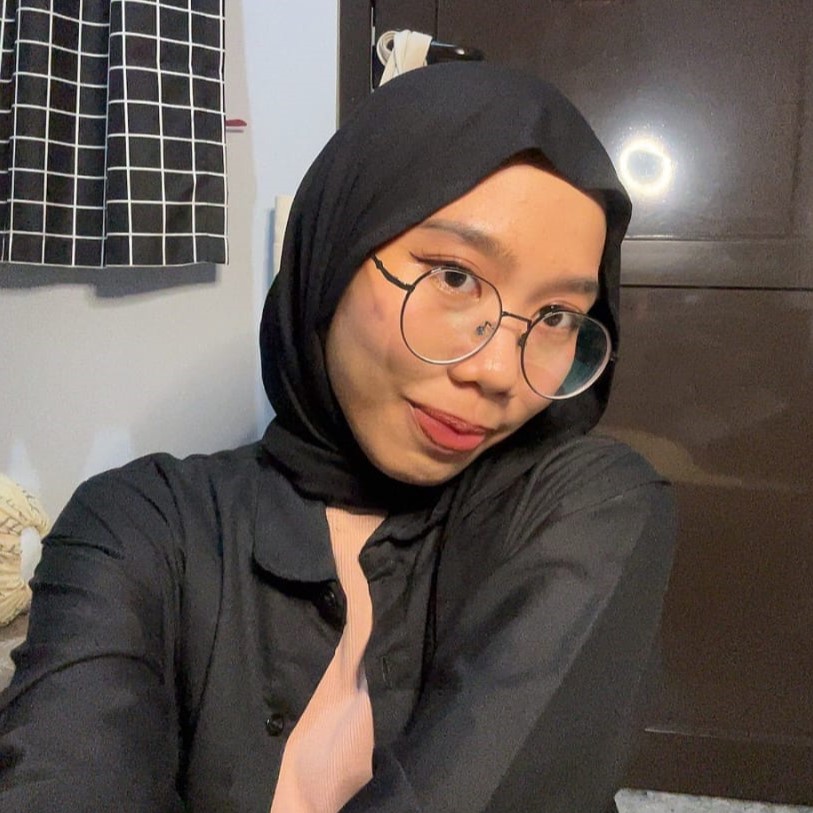
SEO specialist by day, fact-checker by night. An avid reader and content writer dedicated to delivering accurate and engaging articles through research and credible sources.