Before we dive into the world of managing assets, it is important to grasp the basics of deciding between repairing or replacing assets. In many industries, companies often wrestle with this choice: should they fix what they have or invest in something new? This article explores the economic factors behind this decision. By looking at costs and how long assets last, we aim to help readers make smart choices that balance short-term expenses with long-term benefits.
What Does Repairing Assets Mean?
Repairing assets refers to any activity carried out to repair a broken asset to restore full functionality. This process involves fixing or restoring physical items or resources that have become damaged, faulty, or degraded over time.
It can involve repairing machinery, equipment, infrastructure, or other tangible assets to ensure they function properly and efficiently. Repairing assets helps to prolong their lifespan, maintain their functionality, and avoid the need for costly replacements. It is a necessary aspect of asset management aimed at preserving and maximizing the value of valuable resources within an organization or community.
This process is crucial for ensuring that assets continue to contribute to the operations and objectives of an organization or community. By promptly addressing issues and restoring assets to full functionality, businesses can minimize downtime, reduce maintenance costs, and maximize productivity.
What Does Replacing Assets Mean?
Replacing assets refers to acquiring new property by a company or its subsidiaries to replace outdated property of the same type and utility. This process involves removing old or worn-out items and acquiring suitable replacements to fulfill the same purpose or function. It requires careful assessment, selection, and implementation of new assets to meet current requirements.
What Is The Difference between Repairing and Replacing?
In the industrial landscape, repairing involves fixing or restoring damaged or faulty assets to restore their full functionality. This process aims to extend the lifespan of existing assets, minimize downtime, and reduce maintenance costs. On the other hand, replacing involves acquiring new assets to replace outdated, obsolete, or irreparable ones.
Replacing assets is necessary when repairs are no longer feasible or cost-effective, and it aims to improve efficiency, safety, and productivity within the industrial setting. Overall, repairing focuses on maintaining existing assets, while replacing involves upgrading or acquiring new assets to meet evolving needs and standards.
Is It Better To Repair or Replace?
Understanding the importance of conducting a thorough repair or replacement analysis is essential for managing assets effectively. Here are the main steps to follow:
1. Compile Data
Determining whether to repair or replace an asset involves gathering data about its performance and history. This includes reviewing:
- maintenance records
- failure reports
- warranty information
- parts use history
It’s essential to also consult with operators or maintenance staff for their insights on the asset’s condition and performance. For instance, if an industrial conveyor belt consistently experiences motor failures, along with multiple minor issues and staff complaints, it suggests that the asset may be nearing the end of its useful life. By analyzing this data and feedback, you can make an informed decision on whether to repair or replace the asset.
2. Evaluate the Repair Costs
The second step involves assessing the expenses associated with repairing the asset. This includes gathering estimates from maintenance teams or external vendors for parts, labor, and additional fees like shipping. It’s important to consider not only the immediate repair costs but also potential future failures. To estimate future repair costs, review historical records to determine how often the asset has failed in the past and the expenses incurred for each repair. Use this information to calculate the annual repair costs.
For instance, let’s consider a scenario where repairing a conveyor requires $3,500 for parts, $2,200 for labor, and $1,200 for operational downtime, totaling $7,900. If the conveyor has experienced an average of two failures per year over the last two years, the estimated annual repair cost would be $15,800. This calculation helps in deciding whether repairing or replacing the asset is the better option.
Step 3: Consider Replacement Costs
Determining whether to repair or replace involves more than just the initial cost of a new asset. It’s essential to account for additional expenses such as delivery, installation, and training for operators. These extra costs, often overlooked, can significantly affect the total cost of replacement. Moreover, it’s important to assess the expected lifespan and performance of the new asset.
Although a pricier asset may require a higher upfront investment, it might offer features or efficiencies that justify the added expense. For instance, let’s say a new industrial machine costs $20,000, with an additional $3,000 for delivery and installation, and $2,000 for training and transitional downtime. The total replacement cost would amount to $25,000.
4. Consider Operational Impacts and Other Factors
After estimating costs, it’s crucial to weigh other factors affecting your decision. These include how downtime and safety risks could affect operations and finances, as well as how the asset fits into your overall workflows.
Also, think about opportunity costs. Could the money spent on a new asset be used more effectively elsewhere? Conversely, could a new asset bring efficiencies that justify the investment?
An asset prone to frequent failures can disrupt production schedules, lead to overtime, missed deadlines, and decreased morale among employees. These downstream effects ultimately incur costs.
For instance, a conveyor causing frequent unplanned downtime may have a more significant impact on your business than investing in a new conveyor. Additionally, if a failing motor poses safety risks to operators, legal and safety considerations must be taken into account.
5. Make The Decision
In the end, the decision to repair or replace an asset should be carefully considered, taking into account both short-term and long-term factors. It’s not just about choosing the cheapest option, but rather the one that sets your organization up for long-term success.
For instance, if repairing a piece of equipment costs $4,000 and replacing it costs $12,000, you should weigh the potential benefits over time. If the repair can extend the equipment’s life by several years without recurring issues, it may be worth it.
However, if the asset has ongoing problems due to age or environmental factors, and requires frequent costly repairs, replacing it might be the more cost-effective choice in the long run. Ultimately, the decision should align with your organization’s goals and priorities, ensuring optimal performance and efficiency. This marks the final step in the decision-making process.
In conclusion, understanding the decision-making process between repairing and replacing assets is crucial for effective asset management. By carefully assessing factors such as cost, longevity, and ongoing maintenance needs, organizations can make informed decisions that optimize performance and maximize value. It’s not just about choosing the cheapest option but rather the one that aligns with long-term goals and ensures operational efficiency.
To enhance your understanding and proficiency in asset management decision-making, I recommend considering training programs offered by PetroSync. These courses includes:
- ISO 55000 training
- CMRP training
- CRE training
- Applied Reliability Centered Maintenance training
- Root Cause Analysis training
We provide comprehensive knowledge and practical skills to make informed decisions in asset management. By investing in your professional development through PetroSync training, you can gain the expertise needed to navigate complex asset management challenges and drive organizational success.
Credit header image: Freepik
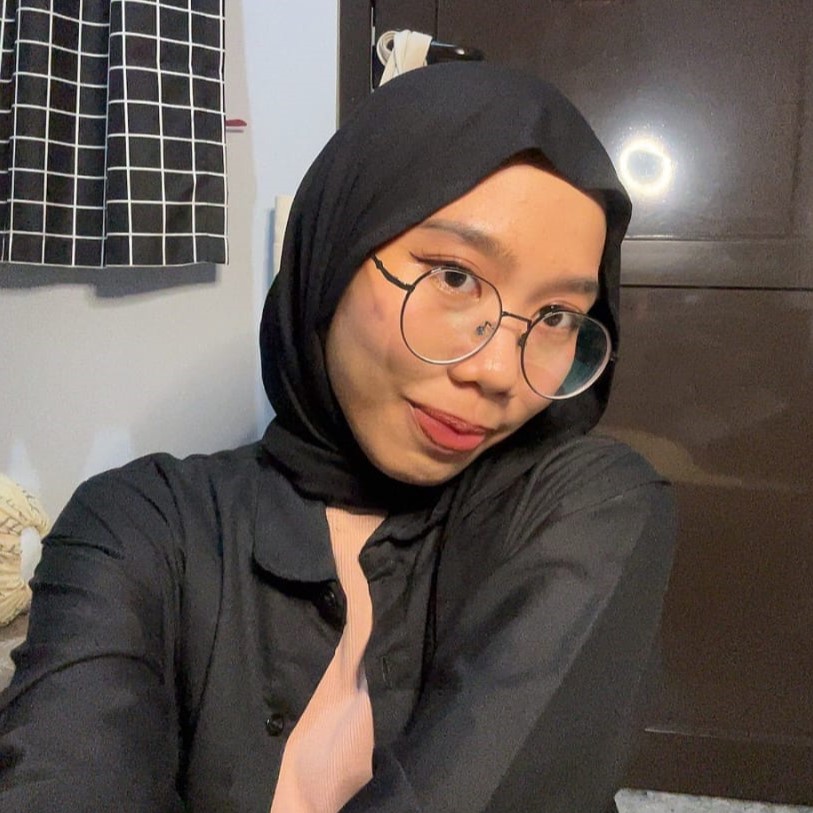
SEO specialist by day, fact-checker by night. An avid reader and content writer dedicated to delivering accurate and engaging articles through research and credible sources.