Storage tanks play a significant role in the oil and gas industry. Since the safety and efficiency of storage tank construction are crucial, American Petroleum Institute (API) has developed standards that provide guidelines for the design, fabrication, and erection of welded steel tanks for oil storage. In this article, we will give the definition and discuss deeper the fundamentals of storage tank design and construction in API 650.
What Is API 650?
The API 650 standard is a worldwide recognized specification that covers the design and manufacturing criteria for large welded steel storage tanks. These tanks are widely used to store petroleum products, chemicals, and other dangerous materials. API 650 ensures that tanks are built to withstand internal pressures and environmental variations, ensuring safety and dependability.
Pressure testing is an important aspect of this standard. Once a tank is constructed, it must undergo comprehensive testing to verify structural integrity. This aids in the discovery of tank faults that could lead to failures under operational stress, making it a crucial tool for tank manufacturers and operators.
How Is The Minimum Requirements Regulated in API 650?
The discussion of allowable stress values for welded steel storage tanks’ shell, roof, and bottom design exists under the standard. The allowable stress values depend on the factors that are calculated using equations specified in the standard. Some affecting factors of allowable stress values for shell and roof are:
- Material properties
- Plate thickness
- Tank diameter, and
- Design temperatures
Meanwhile, for the bottom design, the allowable stress values depend on the material properties of the bottom plate, the thickness of the plate, and the type of bottom design. The guidelines ensure the tank can withstand the loads and stress it will encounter during its lifespan.
What Is The Temperature Limit For API 650?
Temperature is an important factor in pressure testing and operating API 650 storage tanks. API 650 storage tanks are intended to operate within defined temperature ranges to ensure material performance and structural integrity. According to the specification, depending on the materials used in construction, these tanks may withstand temperatures ranging from -40°F (-40°C) to 500°F (260°C).
This wide temperature range allows for the safe storage of a variety of products, including cryogenic liquids and high-temperature chemicals. It is important to note that exceeding these temperature limits during testing or operation can jeopardize the tank’s structural integrity, resulting in fractures, deformities, or other issues. As a result, maintaining the right temperature during pressure tests is important to the tank’s long-term durability.
How Is Material Selection Regulated in API 650?
The material selection for the tank shell in API 650, is determined by considering the material’s strength, toughness, and resistance to corrosion. According to the standard, the shell plate should be constructed using carbon or low alloy steel, and the maximum carbon content must not exceed 0.21%.
The toughness and weldability of the material can be affected by the carbon content, and an increase in carbon content can lead to a higher risk of cracking during welding. The standard permits a broader selection of roof and bottom plate materials, including carbon or low alloy steel, stainless steel, and aluminum. Several factors, such as corrosion resistance, the operation temperature, and the cost, determine the material choice.
What Is The Impact Test Requirement in API 650?
API 650 requires an impact test on materials’ weld metal, HAZ, and base metal with an MDMT lower than the minimum expected operating temperature. The test aims to assess the material’s toughness and ability to resist fracture when exposed to low-temperature conditions. The minimum required impact energy and the test temperature vary depending on the material’s MDMT and thickness.
What Is The Impact Test Result in API 650?
The thickness of the material and the tank temperature are designed to withstand the minimum standards for impact testing results. The minimum energy absorption values required are greater for thicker materials and lower design temperatures. If the impact test results do not meet the predetermined requirements, further evaluations or changes may be required to confirm the material’s appropriateness for the desired use.
How Are Storage Tanks Calculated in API 650?
In the standard, storage tanks are calculated based on specific design criteria, including shell thickness calculations, bottom plate thickness calculations, roof plates calculations, and nozzle openings calculations.
1. Shell Thickness Calculations
Section 5.6.3.2 of API 650 provides a formula that enables the calculation of the minimum required thickness for the tank’s shell. The formula utilizes the design stress, which is determined by the yield strength of the material, joint efficiency, and design temperature. Moreover, the formula considers other factors, including the tank’s hydrostatic test pressure, corrosion allowance, and maximum allowable working pressure (MAWP).
2. Bottom Plate Thickness Calculations
The bottom plate thickness calculations consider the highest level the liquid can reach and how much weight the tank will hold. The standard also gives rules for designing the annular plate, which is the ring-shaped plate that connects the bottom plate to the rest of the tank.
The thickness of the annular plate is determined by how much weight the tank will hold and how hot or cold the environment will be.
3. Roof Plates Calculations
API 650 describes a method for calculating the thickness of a welded steel oil storage tank’s roof plate in Section 5.6. This process involves figuring out the weight of the roof, any equipment on it, and external factors like wind and snow.
Once the design loads are determined, the roof plate thickness can be calculated based on the anticipated temperature changes the tank will experience, which can cause the steel to expand or contract. This information is important because it ensures that the roof can support its own weight and any additional loads while also accounting for temperature changes.
4. Nozzle Openings Calculations
Nozzle openings are crucial components of API 650-compliant welded steel oil storage tanks, providing access points for equipment such as pipes, valves, and instruments. The standard guides the determination of the size and location of nozzle openings, with nozzle size being calculated based on equipment, flow rate, and pressure drop.
This involves determining the maximum flow rate and pressure drop across the nozzle, with the API 650 providing equations to determine the necessary nozzle size.
What Are API 650 Requirements for Storage Tank Fabrication, Erection, NDT, and Leak Testing?
The standard prescribes specific requirements for the materials used in building storage tanks, the welding procedures used during construction, and the qualifications needed for welders and welding procedures. Furthermore, the standard also regulates NDT techniques, such as radiographic, ultrasonic, magnetic particle, and liquid penetrant testing.
Leak testing is also necessary using hydrostatic, pneumatic, or vacuum testing. API 650 also specifies erection requirements such as foundation design, tank elevation, and anchor bolt design. In summary, compliance with the standard guarantees that storage tanks are constructed to high-quality standards and are capable of safely storing their contents.
FAQs about API 650 Standards
Below are some of the most frequently asked questions related to API 650.
What Is The Significance of API 650 Standards?
API 650 standards are vital for ensuring the safe design, construction, and maintenance of above-ground storage tanks, particularly in industries dealing with hazardous substances. They provide guidelines to enhance tank integrity and prevent accidents.
Are API 650 Standards Applicable to All Types of Tanks?
API 650 standards are primarily designed for large, field-erected, above-ground storage tanks. While they may not apply to all tank types, they are crucial for industries where safety and environmental protection are paramount.
How Can I Ensure Compliance with API 650 Standards?
To ensure compliance, it’s essential to engage professionals with expertise in API 650 standards. They can assist in design, fabrication, inspection, and maintenance processes, ensuring that all requirements are met.
What Are The Consequences of Non-Compliance with API 650 Standards?
Non-compliance can result in safety hazards, environmental damage, and legal consequences. It’s imperative for industries to adhere to these standards to protect their assets and the environment.
Can API 650 Standards Be Adopted Internationally?
While the standards are widely recognized and adopted globally, some regions may have their own standards or variations. It’s essential to align with local regulations while adhering to API 650 guidelines.
Are There Any Updates to API 650 Standards?
API 650 standards are periodically updated to reflect industry advancements and safety improvements. It’s crucial to stay updated with the latest revisions to ensure compliance.
If you are an engineer, supervisor, or manager in mechanical engineering and inspection, maintenance and operations, technical and engineering, and corrosion engineering, understanding the fundamentals of the standard is essential.
However, API 653 – Tank Inspection, Repair, Alteration, and Reconstruction training course can be more critical to master since it helps prevent catastrophic failures and protect public safety. PetroSync provides a 5-day training program that focuses on the engineering knowledge required for in-service storage tanks, following the syllabus published by API.
Our API 653 training aims to provide a thorough understanding of the codes, how to interpret them, and develop confidence in making decisions. It prepares you to study the prescribed code and helps you understand its primary intentions.
We also spare a day full of learning API 650 as a commitment to give a comprehensive understanding of API 653 for you. Sculpt your skills for tank inspection, repair, alteration, and rerating pressure vessel systems with PetroSync!
Credit of Header Image: tankstoragemag.com
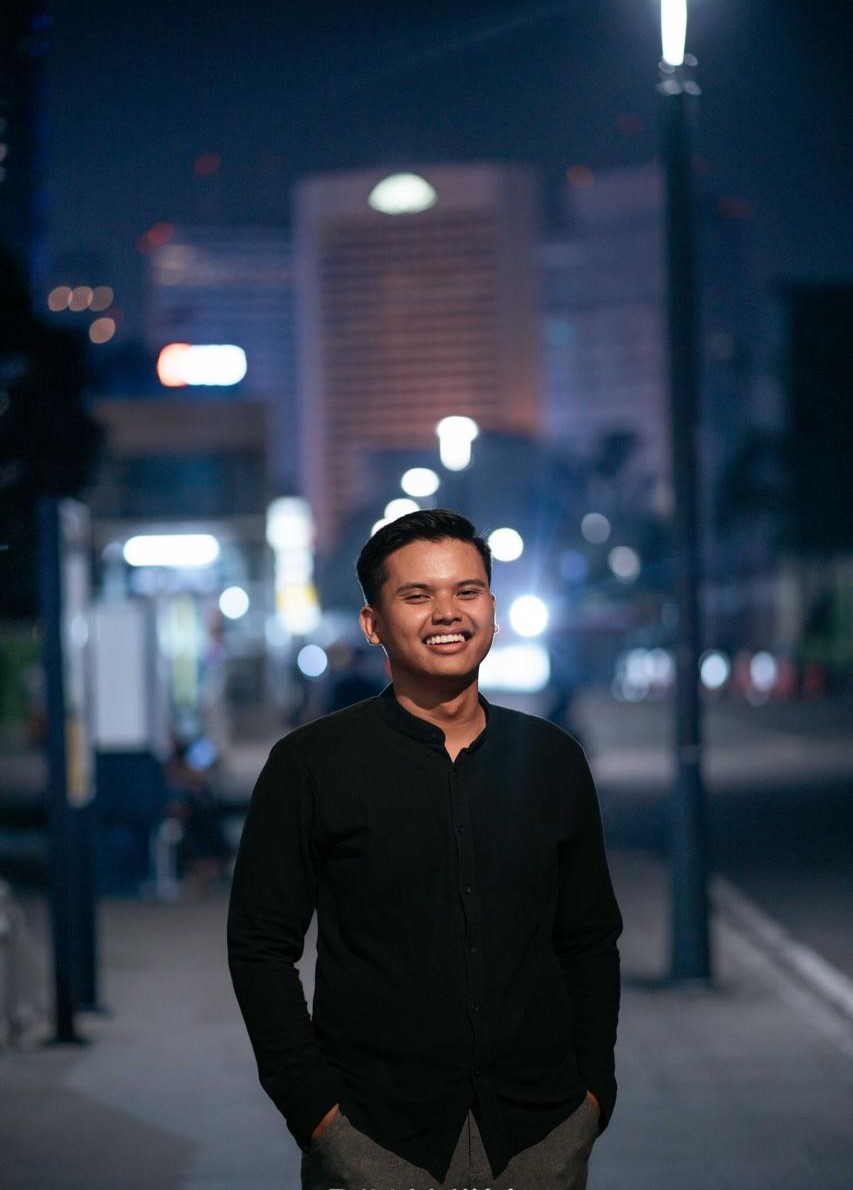
Results-oriented and thorough SEO specialist with extensive experience in conducting keyword research, developing and implementing digital website promotion strategies and plans, managing campaigns to develop company websites in the digital world, excellent knowledge of marketing techniques and principles, and attentive strong attention to detail.