Operator Driven Reliability (ODR) plays a crucial role in how we manage and maintain industrial assets. It’s a program where the people operating the machinery actively participate in keeping those assets working well. Despite its importance in proactive maintenance, some modern industrial facilities have been hesitant to fully embrace ODR. The main goals of the ODR program are simple: to make sure assets are available when needed, to eliminate causes of defects, and to reduce waste. Read on to learn what sets ODR apart from the regular inspection program.
What Is Operator Driven Reliability?
Operator Driven Reliability is an asset management program that involves operators in the maintenance of assets through the execution of inspection routes, where the individuals operating machinery or systems actively participate in ensuring their reliable performance.
It involves operators taking responsibility for regular checks, and minor maintenance tasks, and promptly reporting any issues they observe. This approach empowers operators to play a key role in the reliability and efficiency of equipment, contributing to a safer and more dependable operational environment.
What Are Some Examples of Operator Driven Reliability?
Operator Driven Reliability involves empowering operators to actively participate in the maintenance and upkeep of industrial assets. In industries like oil and gas, petrochemicals, and power, this approach manifests through various tasks.
1. Regular Equipment Inspections
Operators routinely examine machinery for any signs of wear, leaks, or irregularities. This proactive approach helps identify potential issues early on, preventing more significant problems and ensuring the equipment operates reliably.
2. Lubrication Tasks
Operators are responsible for making sure that the moving parts of equipment are properly lubricated. This helps reduce friction and wear, extending the lifespan of components and maintaining the efficiency of the machinery.
3. Tightening and Adjustments
Regularly, operators perform tasks such as tightening bolts and making adjustments to ensure that components are securely fastened and properly aligned. This helps prevent loosening or misalignment issues that could lead to operational problems.
4. Cleaning and Debris Removal
Operators engage in regular cleaning of equipment and removing any debris. This prevents blockages and ensures that the machinery can function smoothly without hindrance.
5. Monitoring Instrumentation
Operators keep a close eye on gauges and instrumentation, promptly reporting any deviations from normal operating conditions. This vigilance helps in maintaining the optimal performance and safety of the equipment.
6. Emergency Shutdown Procedures
Operators undergo training to execute emergency shutdown procedures swiftly in case of abnormal conditions. This quick response is crucial for preventing damage to equipment and mitigating potential hazards.
7. Record Keeping
Operators maintain detailed records of their inspections, maintenance tasks, and equipment performance. This record-keeping is essential for tracking the history of the equipment, analyzing trends, and planning future maintenance strategy and activities to optimize overall reliability.
How To Implement Operator-Driven Reliability?
Implementing Operator Driven Reliability (ODR) in the workplace offers significant advantages, such as reducing blame culture and enhancing overall reliability. To successfully introduce ODR to your organization, there’s no one-size-fits-all approach, as different organizations follow varying methods.
It’s crucial to align the chosen approach with the organization’s workforce. Here are some fundamental tips for implementing ODR:
1. Define the Purpose
Clearly understand why you’re developing an ODR – whether it’s to boost productivity, enhance reliability, or free up maintenance technicians. Prioritize objectives that align with overall organizational goals.
2. Evaluate Current Maintenance Tasks
Examine the preventive maintenance (PM) tasks currently handled by maintenance technicians. Identify routine tasks suitable for operators to perform efficiently.
3. Communication is Key
Open communication channels within the organization to ensure understanding and cooperation. Emphasize the importance of the ODR program to all stakeholders.
4. Categorize Tasks
Depending on the complexity of the ODR program, categorize tasks to facilitate a smoother implementation process. This breakdown helps assign responsibilities more effectively.
5. Form a Cross-Functional Team
Establish a team with representatives from operations, maintenance, and reliability. This leadership-driven team ensures a comprehensive approach to ODR implementation.
6. Document Existing Procedures
Document existing predictive and preventive maintenance procedures and integrate them into the ODR program. This step ensures a seamless transition and avoids duplication of efforts.
7. Continuous Refinement
Treat the ODR program as an ongoing process that contributes to the overall maintenance strategy. Regularly refine the program based on feedback, performance data, and evolving organizational needs.
8. Technology Integration
Recognize that an effective ODR program benefits from leveraging advanced technology in the workplace. Explore and incorporate suitable technologies that align with the organization’s goals.
9. Maintain Technician Involvement
Remember that ODR does not replace complete maintenance. Maintenance technicians should remain an integral part of the process, ensuring a balanced and comprehensive approach.
By following these basic tips, organizations can smoothly implement ODR, fostering a collaborative and efficient approach to maintenance tasks.
In summary, Operator Driven Reliability (ODR) plays a crucial role in managing assets effectively. ODR involves operators actively participating in maintaining industrial assets, creating a culture of shared responsibility. Its importance lies in reducing blame and improving overall reliability.
Implementing ODR requires careful consideration of organizational goals, clear communication, and a systematic approach to task planning. It is an ongoing process that benefits from continuous improvement and the use of advanced technologies.
As organizations aim for greater efficiency, ODR proves to be a strategic and practical approach, emphasizing the role of operators in ensuring optimal performance and longevity of critical assets. Ultimately, ODR contributes to a safer and more reliable operational environment, aligning with the broader goals of effective asset management in various industries.
Join PetroSync Training to Elevate Your Industry Skills
PetroSync recognizes the paramount importance of effective asset management in today’s industrial landscape. As you navigate the complexities of managing assets in your organization, understanding the principles outlined in ISO 55000 can significantly enhance your skills and contribute to the overall success of your operations.
PetroSync, a trusted provider of professional training, invites you to consider taking our ISO 55000 training program. This comprehensive training will empower you with the knowledge and tools necessary to implement robust asset management practices, aligning with international standards.
By investing in your expertise through PetroSync’s training, you not only advance your professional development but also play a key role in elevating the efficiency and reliability of your organization’s assets.
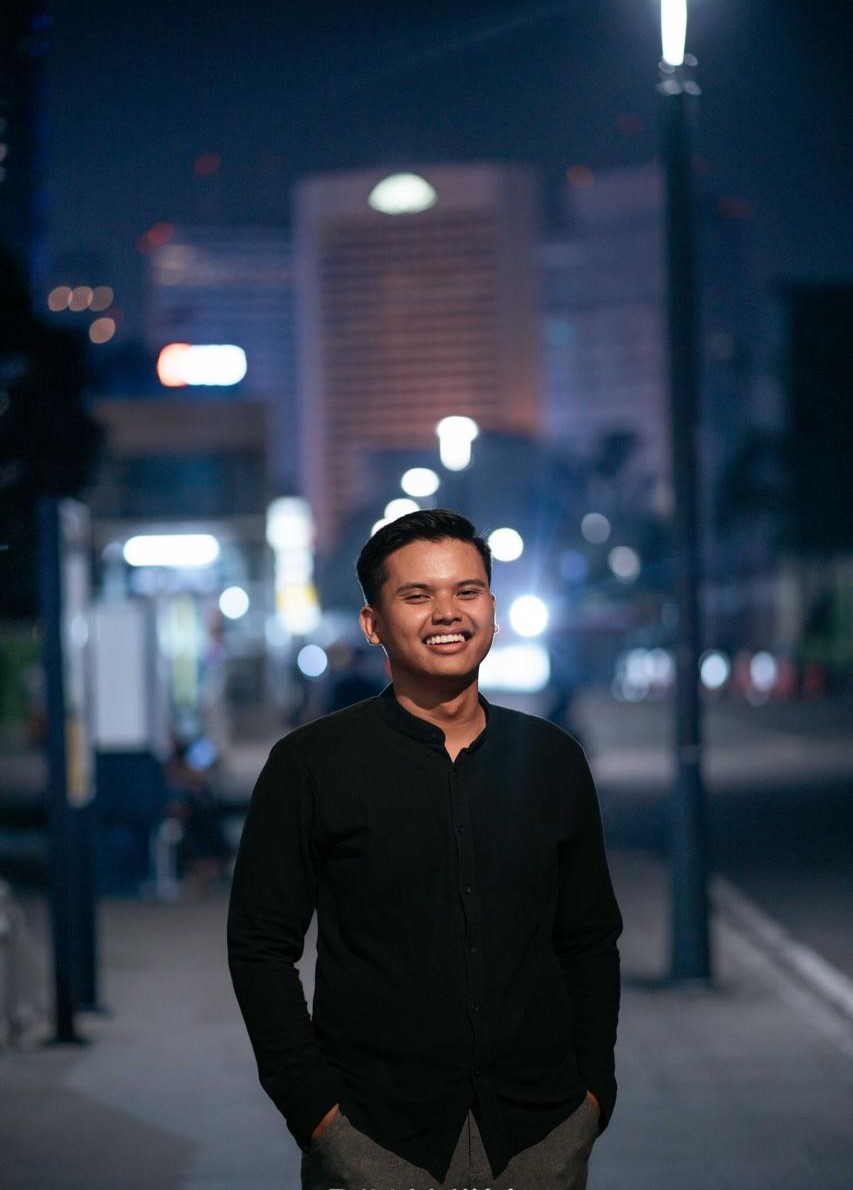
Results-oriented and thorough SEO specialist with extensive experience in conducting keyword research, developing and implementing digital website promotion strategies and plans, managing campaigns to develop company websites in the digital world, excellent knowledge of marketing techniques and principles, and attentive strong attention to detail.