Storage tank inspection is an essential part of the oil and gas industry. However, these tanks can pose significant safety and environmental risks if not adequately inspected and maintained. Regular storage tank inspection can be a critical act to ensure their safety, compliance with regulations, and proper maintenance. In this article, we will discuss the definition, interval and scope, data evaluation, corrosion assessment of the roof, shell, and bottom, and the inspection and testing practices of API 653.
What Is Storage Tank Inspection?
Storage tank inspection gathers important data on tank safety and reliability, helping to extend their lifespan by identifying risks like damage, corrosion, and cracks. The process may involve techniques like visual inspection, non-destructive testing, and corrosion resistance assessment to determine the tank’s structural integrity.
To do storage tank inspection, American Petroleum Institute (API) regulated API 653 to inspect, repair, alter, and reconstruct aboveground storage tanks (ASTs). The guidelines specify the minimum criteria for preserving the tank’s structure, such as the shell, roof, and base. Adhering to API 653 helps guarantee that storage tanks are well-maintained and comply with the required safety and environmental rules.
How Are The Intervals and Scope of Storage Tank Inspections?
According to API 653, the intervals of storage tank inspection are detailed below:
- In-service tanks that have been in service for less than 10 years should be inspected every 5 years.
- In-service tanks that have been in service for 10 years or more should be inspected every 3 years.
- Tanks that have been out of service for some time should be inspected before being returned to service.
- Newly constructed tanks should be inspected before being placed in service.
It’s important to note that these inspection intervals are general guidelines and may need to be adjusted based on the tank’s operating conditions, past inspection results, and other factors. Tank owners and operators should work closely with qualified 653 inspectors and engineers to develop an appropriate inspection and maintenance plan for their specific tanks. Meanwhile, the scope of inspections is explained in the following.
1. External Inspection
This inspection visually examines the exterior of the tank for any signs of corrosion, leakage, or damage.
2. Internal Inspection
In internal inspection, the tank inspector examines the interior of the tank for corrosion, cracking, or other defects that could affect the tank’s integrity.
3. Bottom Inspection
For bottom inspection, it is necessary to check the tank’s floor for settlement, corrosion, or other damage that could impact its stability.
4. Roof Inspection
Inspecting the tank’s roof for signs of corrosion, damage, or deformation is also mentioned under API 653
5. Shell Settlement Inspection
Inspect the tank’s shell for settlement, bulges, or deformations is discussed in the scope of API 653.
6. Hydrostatic Testing
Hydrostatic testing examines the tank’s structural integrity and identify any leaks or weaknesses.
The inspection scope may vary depending on the tank’s design, age, and the substances it stores. It is important to note that API 653 is a minimum standard, and it may be necessary to conduct more frequent or detailed inspections to ensure the tank’s safe and reliable operation.
How to Conduct Data Evaluation and Corrosion Assessment of Roof, Shell, and Bottom Based on API 653?
The evaluation of data and assessment of corrosion are essential elements of the API 653 inspections. These procedures require the examination of different types of data to determine the state of the tank, specifically in terms of its susceptibility to corrosion.
During an inspection of a storage tank, the assessment of the roof is highly important because it shields the tank’s contents from the elements. Inspectors will scrutinize the state of the roof and its constituent parts, such as the roof plates, rafters, and seal welds.
For shell assessment, inspectors will scrutinize the condition of the shell and its parts, including the shell plates, welds, and attachments. While for the bottom assessment, its components, such as bottom plates, welds, and annular plates, are inspected to determine their condition.
How Is The Estimation of The Corrosion Rate in API 653?
API 653 outlines that to estimate corrosion rates, one should consider the following factors:
- Non-destructive testing (NDT) and visual inspection of tank plates
- Historical data on corrosion rates of comparable tanks or materials in similar settings
- An analysis of the tank’s service environment, such as the stored product type, temperature, humidity, and other relevant factors that may impact corrosion rates.
Furthermore, the standard advises using the estimated corrosion rate to assess the remaining lifespan of the tank and to formulate a plan for future maintenance, repairs, or replacements.
What Are The Testing Practices of API 653?
The following testing practices can be conducted according to API 653:
1. Visual Inspections
A visual inspection should be conducted regularly on all tanks to detect any signs of corrosion, leaks, or other damage. The inspection should be performed by a qualified API 653 inspector and should include an examination of the tank’s interior, exterior, and all appurtenances.
2. Hydrostatic Testing
API 653 recommends hydrostatic testing for tanks that have undergone major repairs, alterations, or reconstruction. The tank should be tested at a specified pressure, which should be maintained for a specific period.
3. Vacuum Box Testing
This test can be conducted on the bottom plates of tanks to identify leaks in the welds or shell-to-bottom plate joints. The vacuum box test should be performed after any repairs or alterations.
4. Ultrasonic Testing
Another testing practice is ultrasonic testing. It is a non-destructive method used to detect defects in the tank wall. This method can be used to test the tank shell, roof, and floor, as well as any welds.
5. Magnetic Particle Testing
To detect surface or slightly subsurface cracks or defects in the welds or base metal of the tank, the API 653 inspector can do magnetic particle testing. This test should be conducted on all welds after any repairs or alterations.
It’s important to note that the specific testing practices and frequencies may vary depending on the tank and operating conditions. It’s essential to have a storage tank inspection understanding to determine the appropriate testing practices for your specific tank.
PetroSync offers API 653 – Tank Inspection, Repair, Alteration, and Reconstruction training course that lasts for 5 days providing a thorough explanation of the necessary engineering knowledge for in-service storage tanks, focusing on the syllabus published by API (Body of Knowledge).
Our API 653 training is divided into six main areas, they are basic storage tank design engineering (API 650), in-service inspection techniques (API 653/RP 575/RP 577), damage mechanisms (API 571), cathodic protection (API RP 651), the lining of tank bottom (API RP 652), and retirement thickness calculations.
These areas are crucial for delivering a quality job and ensuring safe operation. You will receive comprehensive course notes, which include practical case studies and the main points of the course to impart knowledge. Let’s avoid unplanned shutdowns and reduce expenses associated with storage tank facilities with PetroSync!
Credit Header Image: news.cgtn.com
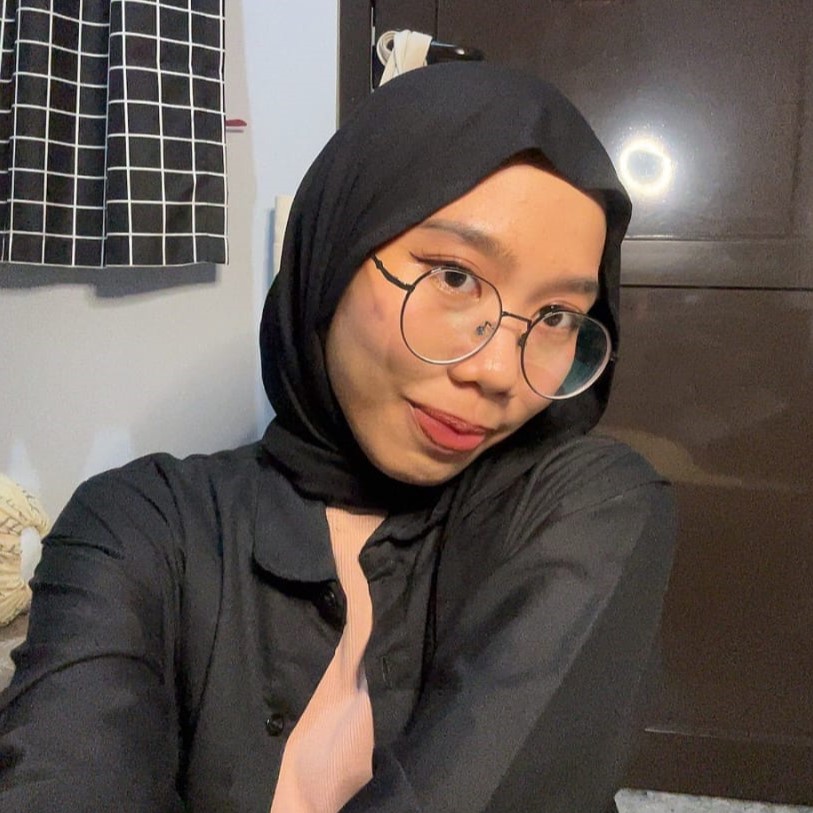
SEO specialist by day, fact-checker by night. An avid reader and content writer dedicated to delivering accurate and engaging articles through research and credible sources.