Having a thorough understanding of damage mechanisms is crucial for damage mitigation and risk-based inspection. Whether it pertains to petrochemicals, chemicals, power plants, or the oil and gas industry, possessing a comprehensive knowledge of the processes and factors that contribute to deterioration is essential for implementing proactive measures and averting potential failures. In this article, we will talk about the fundamentals and types of damage mechanisms that occur in industrial equipment.
What Are Damage Mechanisms in API?
Damage mechanism refers to mechanical, physical, chemical, or any other process that leads to the degradation of materials or equipment over time. Engineers and technicians must identify and understand damage mechanisms to design and maintain safe and reliable structures and equipment.
By recognizing the specific types of damage that are likely to occur under different conditions, they can develop appropriate strategies to prevent or mitigate damage and ensure the longevity and safety of materials and structures. The American Petroleum Institute (API) regulates how damage mechanisms should be addressed.
In API 580, there are guidelines providing risk-based inspection (RBI) and the fundamental principles and practices for establishing an RBI program for fixed equipment and piping in the refining and petrochemical sectors. Within the RBI process, API 580 takes into account diverse damage mechanisms that may impact equipment, including but not limited to, corrosion, fatigue, and brittle fracture.
On the other hand, API 581 deals with base resource documents and focuses on the quantitative evaluation of risk related to damage mechanisms. API 581 offers direction on how to assess the probability and severity of different types of damage mechanisms and how to prioritize inspection tasks based on the level of risk.
What Are The Damage Mechanisms List?
API 580 provides a comprehensive list of potential damage mechanisms, which includes but is not limited to:
1. Corrosion (General, Localized, and Environmentally Assisted)
General corrosion occurs uniformly over the entire surface of a material, leading to a decrease in thickness and strength. Localized corrosion takes place in specific areas like pits or crevices, causing localized damage and increasing the risk of leaks.
Lastly, environmentally assisted corrosion is accelerated by specific environmental conditions, such as high temperature, high pressure, or exposure to certain chemicals.
2. Erosion (Abrasive and/or Corrosive)
Abrasive erosion happens when fluids or particles, like sand or debris, move over a surface and cause physical wear and tear, leading to material loss and thickness reduction. Corrosive erosion, on the other hand, occurs when corrosive substances, like acids or salts, react with the surface of the material, resulting in chemical wear and tear and material loss.
3. Fatigue (Thermal/Mechanical and/or Vibration)
Temperature changes lead to thermal fatigue, which expands and contracts the material, leading to cyclic stresses that can crack and fail the material. Cyclic loading causes mechanical fatigue, which forms cracks and eventually fails the material. Repeated vibration causes vibration fatigue, which generates cyclic stresses that can crack and fail the material.
4. Creep and Stress Rupture
Creep and stress rupture are types of material failure caused by prolonged exposure to high temperatures and stress.
5. Hydrogen-induced Cracking
Hydrogen-induced cracking is when the metal fails due to the presence of hydrogen and stress, resulting in cracks that can eventually cause the material to fail.
6. Sulfide Stress Cracking
Sulfide stress cracking happens when the material fails due to the presence of hydrogen sulfide, tensile stress, and environmental factors like temperature, pH, and chloride concentration.
7. Brittle Fracture
A brittle fracture occurs when the material cracks suddenly and catastrophically, without much plastic deformation. API 580 is a recommended practice that provides guidelines for managing the risk of equipment failure, including the risk of brittle fracture.
8. High-temperature Hydrogen Attack (HTHA)
HTHA is a form of harm that can take place in the equipment utilized in the petrochemical and petroleum refining industries. The cause of this damage is the reaction of steel used in equipment such as pipelines, pressure vessels, and reactors with high-temperature hydrogen gas.
9. Corrosion Under Insulation
Corrosion Under Insulation (CUI) is a frequent issue in the petrochemical and petroleum refining sectors that arises when moisture builds up beneath insulation materials on equipment like tanks, vessels, and pipelines, causing the metal underneath to corrode.
10. Amine-induced Stress Corrosion Cracking
Stress Corrosion Cracking (SCC) induced by amine is a form of corrosion that can happen in equipment used in the petrochemical and petroleum refining industries. The root cause of this corrosion is the reaction of materials susceptible to amine compounds, which are used in processes like gas sweetening and desulfurization, in the equipment.
11. Microbiologically Influenced Corrosion
MIC is a form of corrosion that can take place in the petrochemical and petroleum refining sectors. The underlying reason for this corrosion is microorganisms like bacteria and fungi that reside on the surface of the equipment and create corrosive substances capable of damaging the metal underneath.
12. Galvanic Corrosion
Galvanic corrosion happens when there is contact between two different metals in the presence of an electrolyte. For instance, if steel and copper come into contact with each other and are exposed to an electrolyte like acidic solutions or salt water, this creates a galvanic cell.
13. Flow-accelerated Corrosion
FAC (Flow-Accelerated Corrosion) happens when the speed of a fluid, usually water, boosts the rate of corrosion on the inner side of pipes or machines. The fast movement of the fluid creates turbulence, which eliminates the protective oxide coating on the metal surface and speeds up the process of corrosion.
14. Fire Damage
Fire damage occurs when a fire harms equipment or structures. In API 580, fire damage is one of the potential damage mechanisms that a risk-based inspection must identify and assess. This includes evaluating the chances and effects of fire damage and deciding on suitable inspection and maintenance actions to handle the risk.
15. Stress Corrosion Cracking
When a material is exposed to a corrosive environment and experiences tensile stress, which can result from mechanical loading or residual stress, stress corrosion cracking can occur. This causes cracks to form and spread within the material, ultimately leading to failure.
What Are The Standards That Address Damage Mechanisms?
A thorough examination of damage mechanisms is crucial for developing a reliable inspection plan. When we understand the types of damage and how they appear, those in charge of inspections can choose the best methods for finding, describing, and measuring potential damage. Additionally, they can set up inspection schedules using industry guidelines like mentioned below.
1. API 510 – Pressure Vessel Inspection
API 510 focuses on pressure vessel inspections and includes guidelines for identifying and assessing damage mechanisms in these vessels. It provides criteria for determining the fitness-for-service of pressure equipment.
2. API 570 – Piping Inspection
API 570 is centered around piping inspection, and it outlines procedures for inspecting and evaluating damage mechanisms in piping systems. It ensures the integrity of piping used in various industries.
3. API 653 – Storage Tank Inspection
API 653 primarily deals with the inspection and repair of aboveground storage tanks (ASTs). It covers the identification and assessment of damage mechanisms in ASTs to maintain their safety and reliability.
4. API 571 – Damage Mechanism
API 571 is specifically dedicated to the study of damage mechanisms. It provides detailed information about various damage mechanisms, their characteristics, and how to manage and mitigate them effectively.
5. API RP 579 – Fitness for Service
API RP 579 is a recommended practice for fitness-for-service assessments. It offers guidance on evaluating damage mechanisms and provides acceptance criteria to determine if equipment can continue to be safely operated.
6. API 580 and API 581 – Risk Based Inspection
These standards focus on risk-based inspection (RBI). API 580 provides the principles and practices for implementing RBI, while API 581 offers quantitative methodologies for assessing the risk of damage mechanisms. Together, they help prioritize inspection efforts based on risk, ensuring a cost-effective approach to asset integrity management.
What Are Some FAQs Related to Damage Mechanism?
When it comes to damage mechanisms, there are several frequently asked questions related to the issue.
1. How Often Should Equipment Be Inspected for Damage Mechanisms?
The frequency of inspections depends on several factors, including the type of equipment, the nature of the process, and the history of damage mechanisms. However, inspections are typically conducted annually or biannually.
2. Can Damage Mechanisms Be Completely Eliminated?
While it’s challenging to completely eliminate damage mechanisms, they can be effectively managed and mitigated through proper inspection, maintenance, and material selection.
3. Are There Industry Standards for Mitigating Damage Mechanisms?
Yes, various industry standards, including API 571, provide guidelines for mitigating damage mechanisms and ensuring the integrity of industrial equipment.
4. What Are Some Common Materials Used to Resist Damage Mechanisms?
Materials like stainless steel, alloy steel, and corrosion-resistant coatings are often used to resist damage mechanisms.
5. How Can I Learn More About Damage Mechanisms following API 571?
To delve deeper into this topic, consider attending industry seminars, workshops, and consulting with experts in the field.
Knowing the types of damage mechanisms and how to perform correct assessments play a crucial role in identifying potential causes of equipment failure and developing effective mitigation strategies to manage the associated risks. Engineers must address damage mechanisms to ensure safe and efficient equipment operation, especially in the oil and gas industry, where failure can result in severe consequences such as loss of life, environmental damage, and significant financial losses.
The understanding of damage mechanisms is essential in the context of reliability-centered maintenance. You can opt for RCM approach to develop effective maintenance strategies and enhance equipment reliability by joining Applied Rieliability Centered Maintenance.
Furthermore, we also have API 571 – Damage Mechanisms training course that is invaluable for those looking to gain an in-depth understanding of damage mechanisms in the oil and gas sector. PetroSync’s training is specifically designed to equip engineers with the essential knowledge and skills needed to recognize, assess, and mitigate the risks associated with various damage mechanisms.
This training offers significant benefits to you. If you are an engineer, supervisor, manager, or individual responsible for implementing damage mechanism assessments within your organizations or plant facilities. This includes those in charge of mechanical integrity, equipment reliability, and inspection personnel tasked with ensuring the efficient and cost-effective inspection of process plant equipment.
We believe that our API 571 training can provide you with the expertise required to identify and mitigate risks effectively, all while enhancing your professional standing. Join us now and hone your inspection skills with PetroSync!”
Credit header image: freepik.com
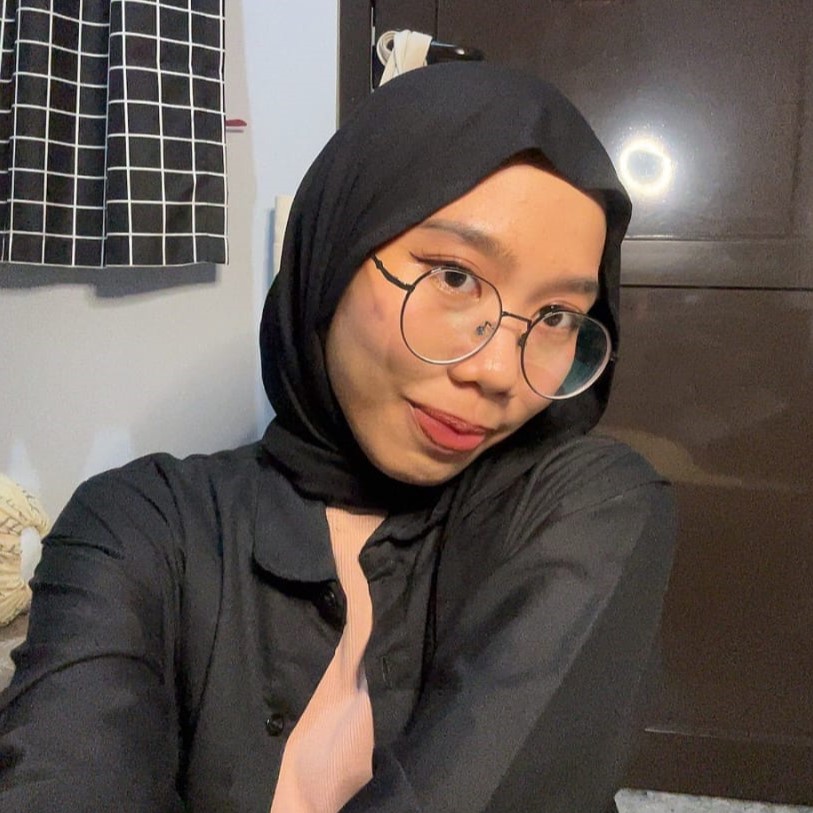
SEO specialist by day, fact-checker by night. An avid reader and content writer dedicated to delivering accurate and engaging articles through research and credible sources.