In the industrial operations, the meticulous practice of Maintenance Inspection stands as a cornerstone for ensuring the smooth functioning of machinery and equipment. This article delves into the essential aspects of Maintenance Inspection as a way to provide you with a straightforward understanding of its types, examples, and best practices.
What Is Maintenance Testing and Inspections?
Maintenance testing and inspections are essential practices carried out to ensure the ongoing functionality and reliability of machinery and equipment in various industrial settings. The process involves systematic examinations and assessments of equipment to identify potential issues, while inspections focus on visually examining components and systems for signs of wear, damage, or other abnormalities.
These proactive measures aim to catch problems early, preventing unexpected breakdowns and minimizing downtime. By conducting regular maintenance testing and inspections, organizations can extend the lifespan of their assets, enhance safety, and optimize operational efficiency.
What Is The Difference Between Preventive Maintenance and Inspection?
The difference between preventive maintenance and inspection lies in their primary objectives and approaches. Preventive maintenance is a proactive strategy aimed at avoiding potential issues by regularly servicing equipment, replacing worn-out parts, and conducting scheduled tasks to prevent breakdowns.
On the other hand, inspection is a focused examination process that involves visually assessing equipment components for signs of wear, damage, or abnormalities. While preventive maintenance is more comprehensive and involves pre-planned activities, inspections specifically target the visual condition of the equipment. Both practices, however, contribute to the overall goal of maintaining machinery reliability and minimizing unexpected failures.
What Are The Benefits of Doing Maintenance Inspection?
Performing maintenance inspections offers several notable benefits in ensuring the smooth operation and longevity of machinery and equipment. Firstly, it allows for the early identification of potential issues, enabling timely intervention to prevent more significant problems from arising.
Additionally, maintenance inspections contribute to the overall safety of the workplace by identifying and addressing potential hazards. Regular inspections also play a key role in minimizing unexpected breakdowns, reducing downtime, and extending the lifespan of equipment.
Moreover, by detecting and resolving issues promptly, organizations can optimize operational efficiency and avoid costly repairs or replacements. In essence, the benefits of maintenance inspections encompass enhanced safety, prolonged equipment life, and increased operational reliability.
What Are The 9 Types of Maintenance Inspections?
In this section, we will explore some of the maintenance inspections that play pivotal roles in ensuring the efficiency, safety, and longevity of industrial and building systems.
1. Safety Inspections
Safety inspections focus on assessing the workplace environment to identify potential hazards or unsafe conditions. This includes examining equipment, tools, and infrastructure to ensure compliance with safety standards and protocols, and fostering a secure working environment.
2. Failure-finding Inspections
Failure-finding inspections aim to proactively identify potential failures or weaknesses in equipment. By conducting thorough examinations, organizations can catch and address issues before they lead to unexpected breakdowns, minimizing disruptions.
3. HVAC Inspections
HVAC inspections concentrate on heating, ventilation, and air conditioning systems. Regular assessments of these systems ensure they operate efficiently, providing a comfortable and controlled indoor environment while also preventing energy wastage.
4. Lighting Inspections
Lighting inspections involve evaluating the condition and functionality of lighting fixtures. This ensures proper illumination for safety, productivity, and energy efficiency. Any damaged or inefficient lighting elements can be addressed promptly.
5. Electrical Inspections
Electrical inspections focus on the examination of electrical systems, wiring, and components. Detecting potential issues early on helps prevent electrical failures, ensuring the safety of personnel and the integrity of equipment.
6. Building Interior Inspection
Building interior inspections cover a comprehensive assessment of interior spaces. This includes checking for structural integrity, identifying potential maintenance needs, and ensuring a safe and comfortable environment for occupants.
7. Building Exterior Inspection
Building exterior inspections involve evaluating the external components of a structure. This includes checking for signs of wear, damage, or structural issues, safeguarding against external elements and preserving the building’s overall integrity.
8. Plumbing Inspection
Plumbing inspections focus on assessing the functionality of plumbing systems. This includes checking for leaks, corrosion, or any potential issues that may compromise water supply or drainage, maintaining a hygienic and efficient plumbing infrastructure.
9. Fire Protection Inspection
Fire protection inspections concentrate on evaluating fire safety measures. This involves checking fire alarms, extinguishers, and other protective systems to ensure they are in optimal condition, mitigating the risk of fire hazards.
By conducting these types of maintenance inspections, organizations can systematically address various aspects of their facilities, promoting safety, efficiency, and the overall well-being of the workplace.
In conclusion, maintenance inspections emerge as the linchpin in sustaining the optimal functionality and safety of diverse industrial and building systems. Through meticulous examinations, early issue identification, and proactive interventions, organizations can fortify the resilience of their equipment and structures.
These inspections not only minimize unexpected breakdowns, reduce downtime, and extend the lifespan of assets but also foster a secure working environment. As a cornerstone of preventive maintenance, regular inspections empower organizations to navigate challenges effectively, enhancing operational efficiency and ensuring the longevity of their investments.
Now, as you grasp the significance of maintenance inspections, consider further enhancing your expertise by exploring the comprehensive Maintenance and Reliability training programs offered by PetroSync. These courses are designed to deepen your understanding of crucial aspects in the maintenance and reliability domain, empowering you with valuable insights and skills.
PetroSync provides a range of training sessions, including ISO 55000 training, which delves into the international standards for asset management, ensuring you are well-versed in optimizing asset performance.
Additionally, you can explore Reliability Centered Maintenance (RCM) training, which focuses on developing strategies to maintain the reliability of assets effectively. Root Cause Analysis (RCA) training equips you with the tools to identify and address the underlying causes of problems, promoting a proactive approach to troubleshooting.
Furthermore, PetroSync offers Certified Maintenance and Reliability Professional (CMRP) training, where you can enhance your knowledge and proficiency in various aspects of maintenance and reliability. The Certified Reliability Engineer (CRE) training is tailored to those seeking to deepen their expertise in reliability engineering principles.
Whether you’re looking to broaden your understanding of Root Cause Analysis or seeking specialized training in ISO standards, PetroSync‘s courses provide a valuable platform to expand your skill set and contribute effectively to the realm of maintenance and reliability.
Credit header image: Pexels
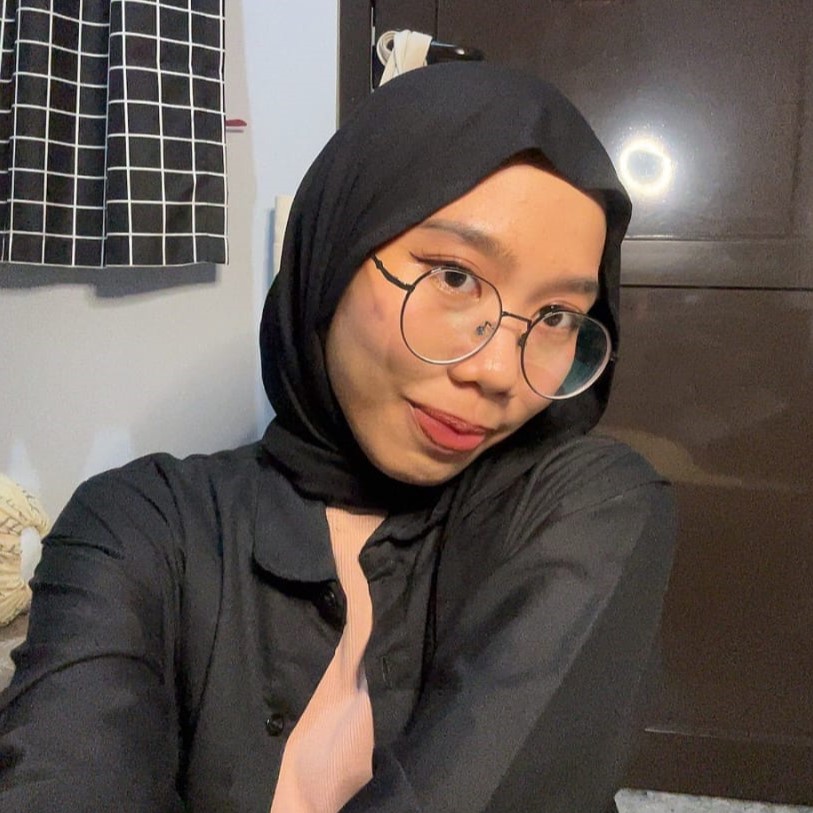
SEO specialist by day, fact-checker by night. An avid reader and content writer dedicated to delivering accurate and engaging articles through research and credible sources.